
2015 Ontario Stove Testing Camp
July
9 - 10, 2015
with Crispin
Pemberton-Pigott
photo
story by Norbert Senf
Back to Lopez Labs
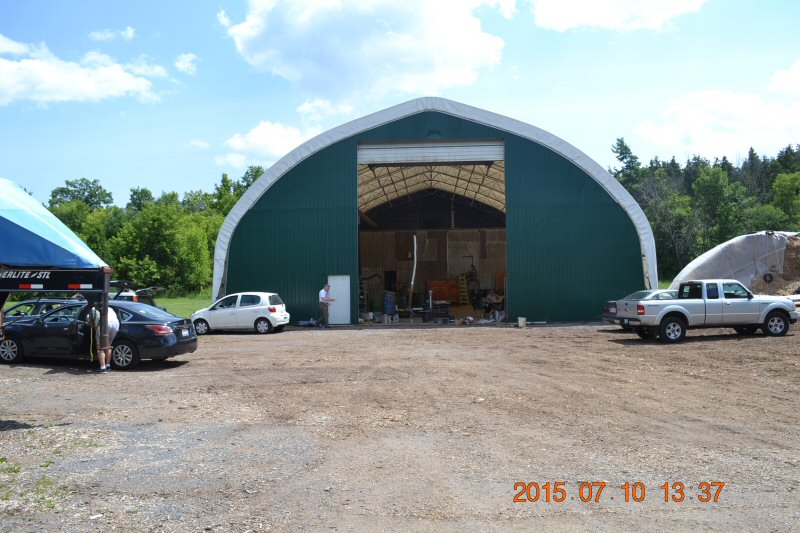
The
camp took place at Burt's Greenhouses near
Kingston ON.
This
is the shed that holds the 1.25 Megawatt chip fired boiler system.
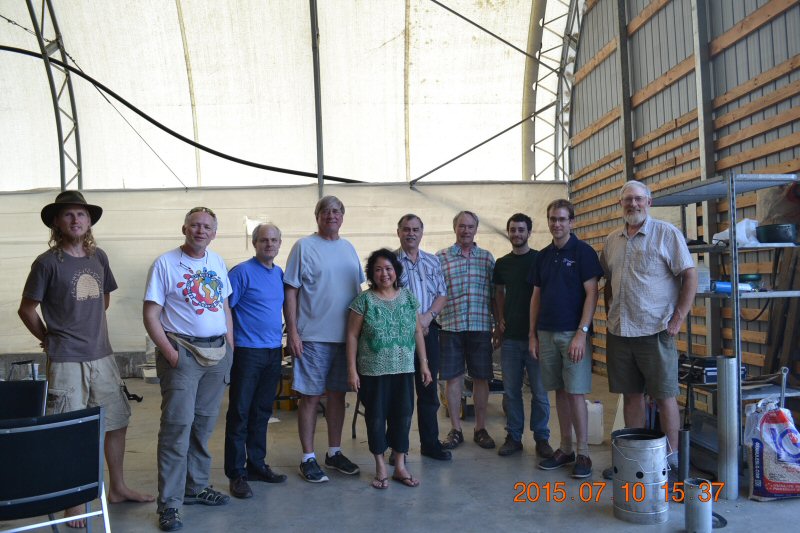
Attendees
came from as far away as New Mexico and Norway
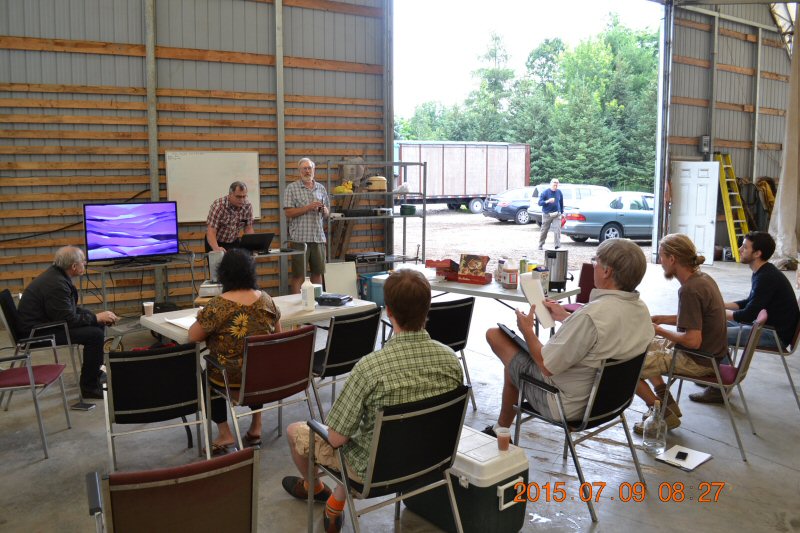
Alex
English, who runs the boilers at Burt's, introduces Crispin
Pemberton-Pigott from New
Dawn Engineering

We
started with a live burn to demonstrate the concepts of a natural
draft, top-lit updrafting gasifier (ND-TLUD)
In
this view the stove is upside down, showing the primary air inlet beneath the fuel bed.
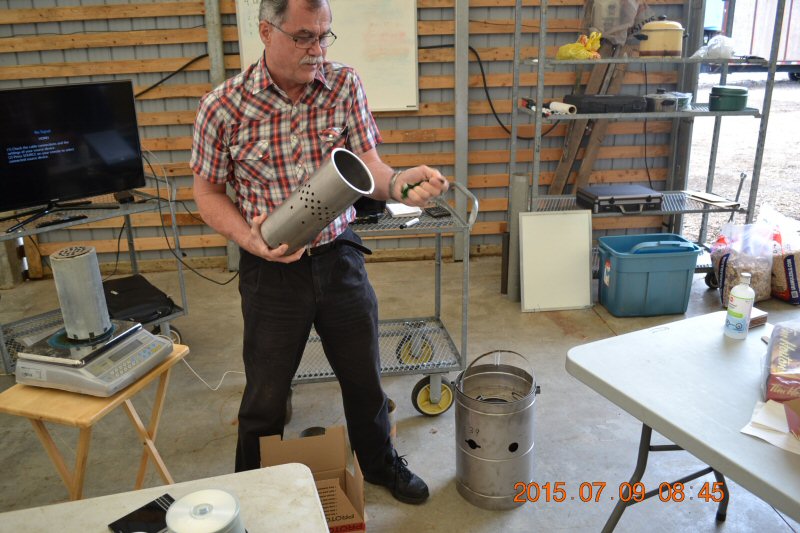
The
burn chamber sits inside an outer sleeve that is used to preheat the
secondary air.
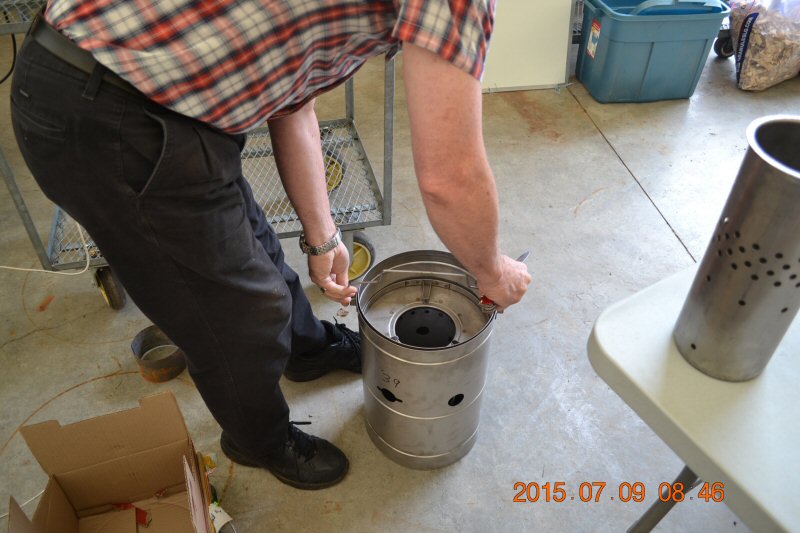
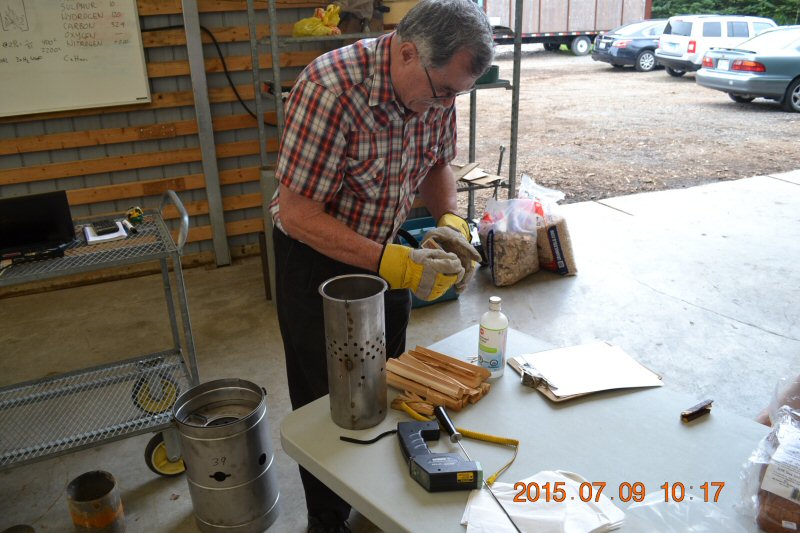
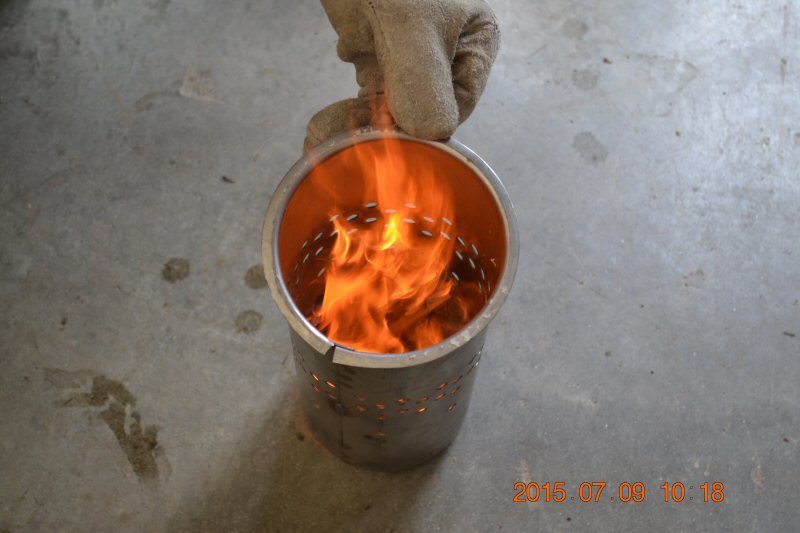
Secondary
air holes at the top. Notice the initial long flaming of the wood gases.
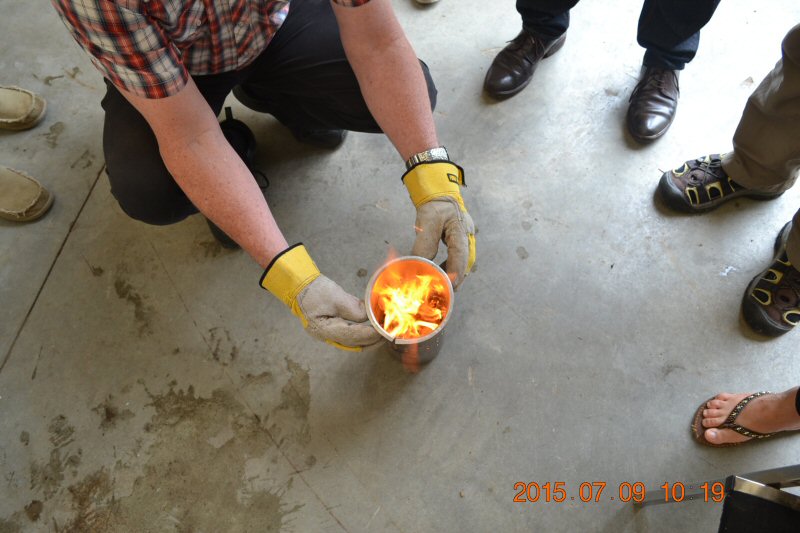
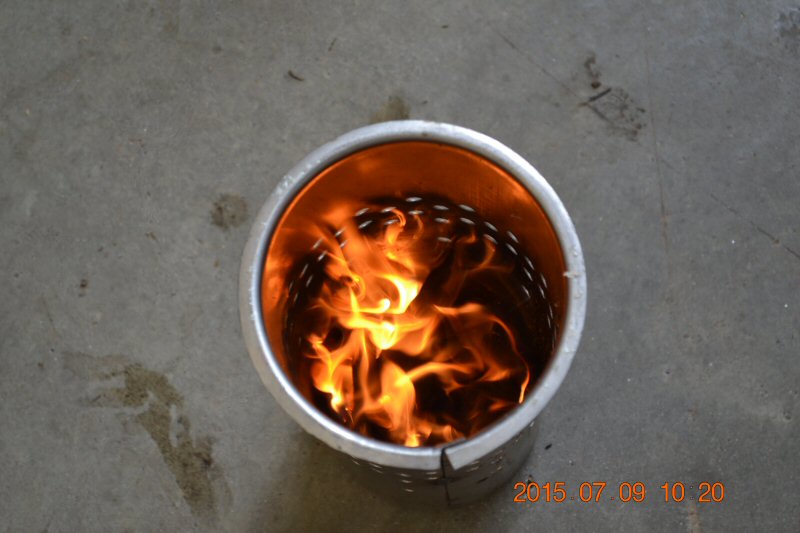
As
the wood burns down to char at the bottom, the flaming is shorter and
happens at the secondary air inlets.
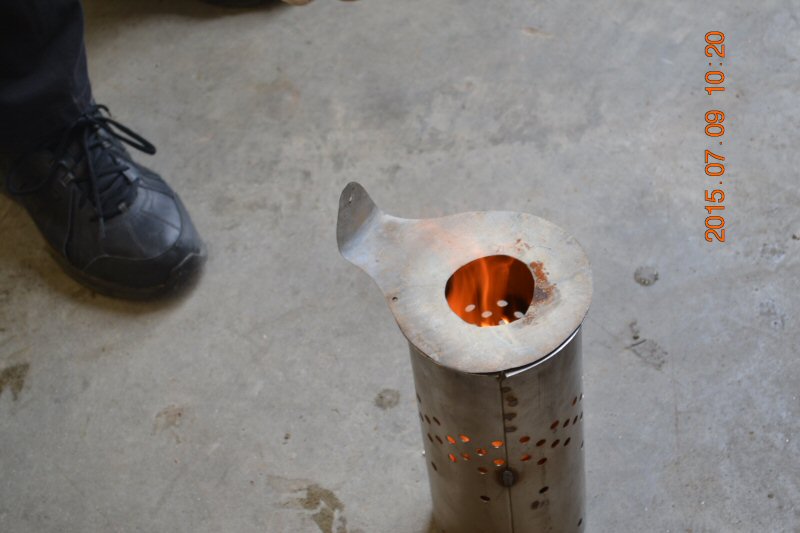
A
restrictor to prevent cold air downdrafting in the tube.
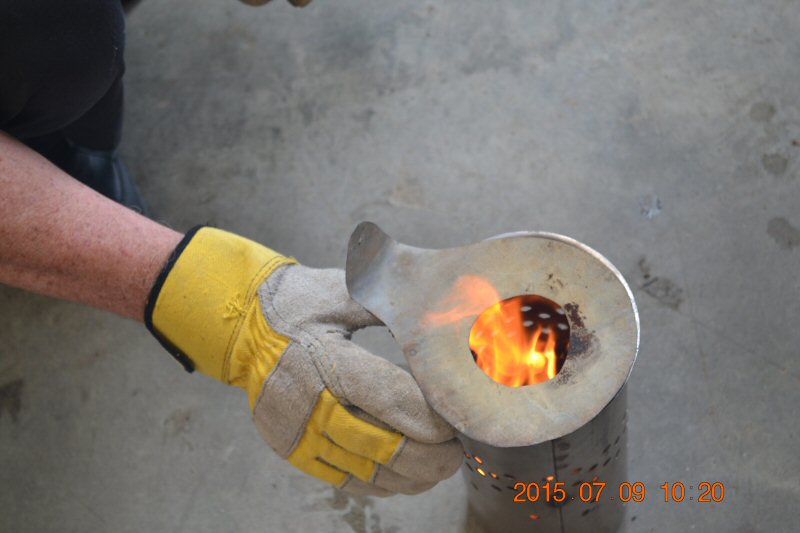

An improved stove that Crispin designed for Mongolia to burn the local lignite coal, achieved a particulate emissions reduction of 99.9%,
A stove changeout program reduced the heavy air pollution in the Mongolian capital of Ulaanbaatar by 65%
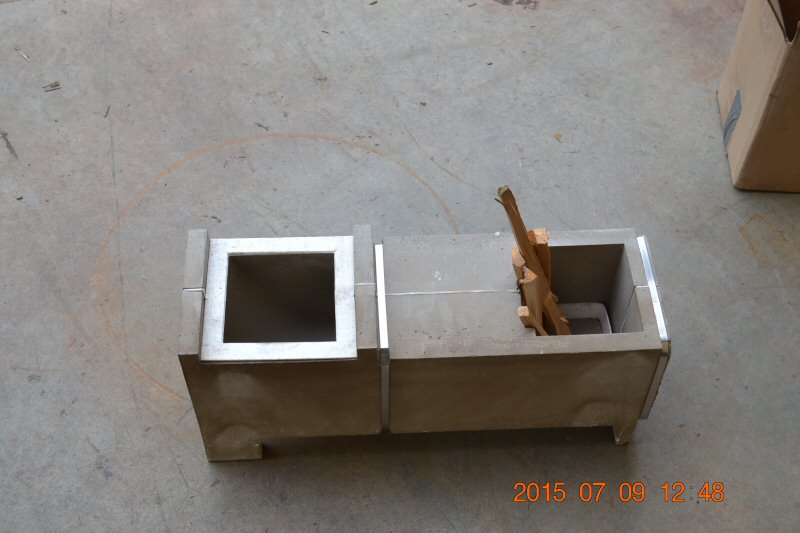
MHA
member Andrew Brunning attended the workshop, and brought down this
precast rocket firebox.
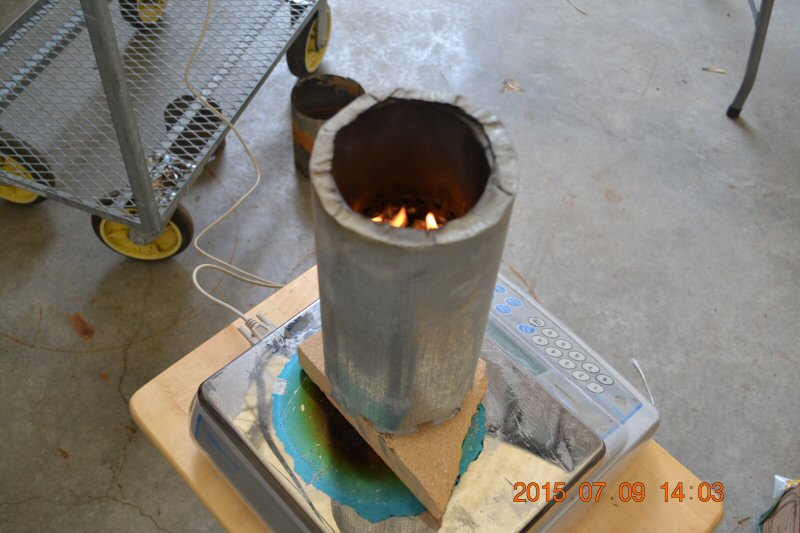
A
$1.00 stove developed by Crispin for Haiti. It is sitting on a digital
scale that measures the weight loss from the fuel in order to
determine
the burn rate and power output in real time.
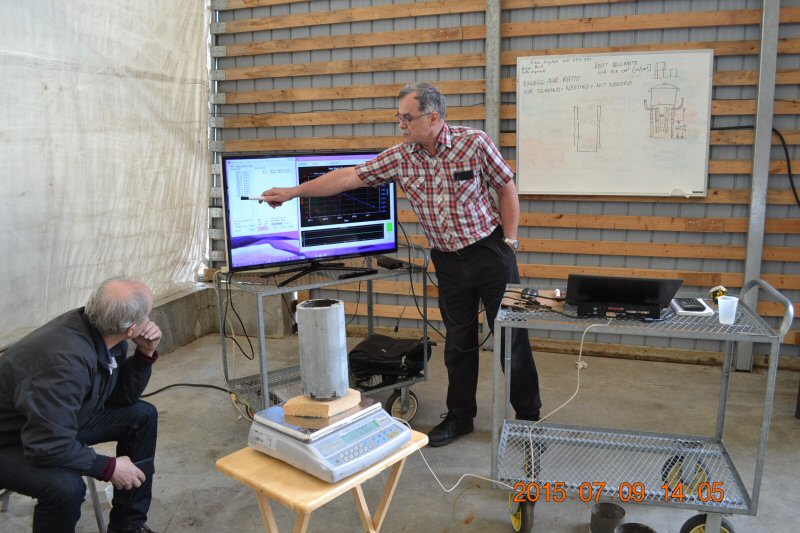
To the left is Jan Sorensen from Norway, who manufactures stoves in Zambia, and is involved in a biochar project there.
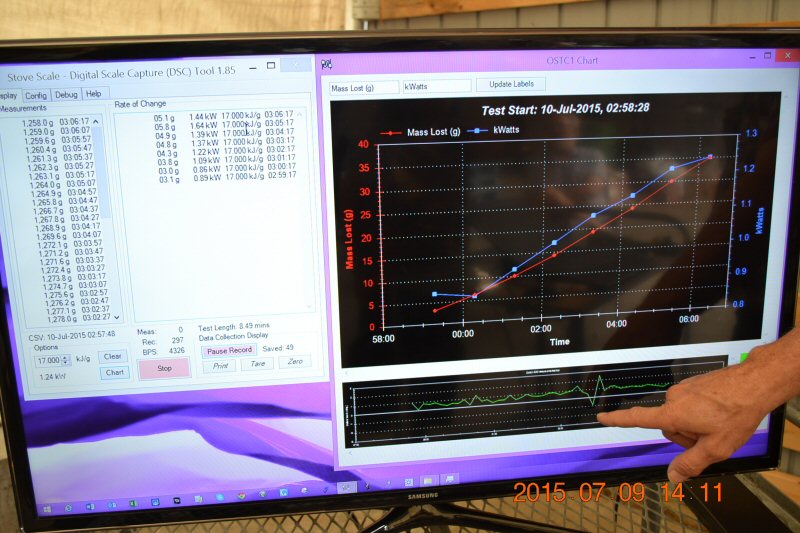
This
custom software takes data from the scale and converts it for stove
testing use.
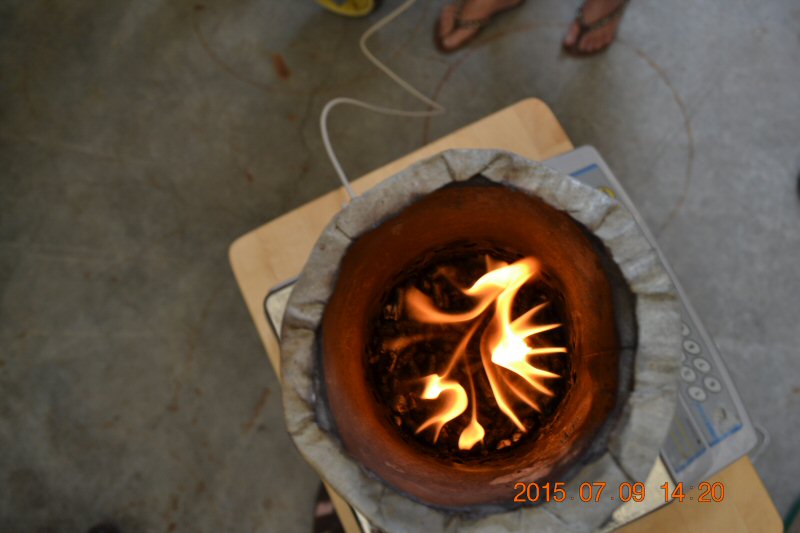
Notice
the flamelets at the secondary air holes.
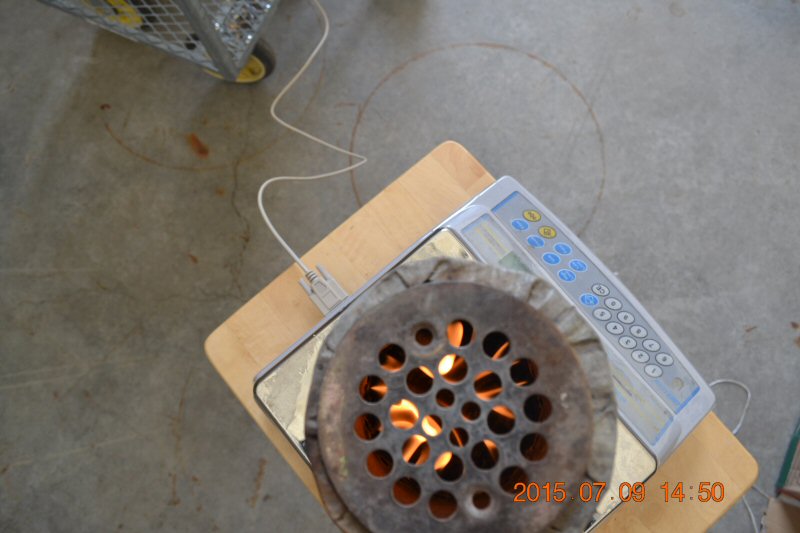
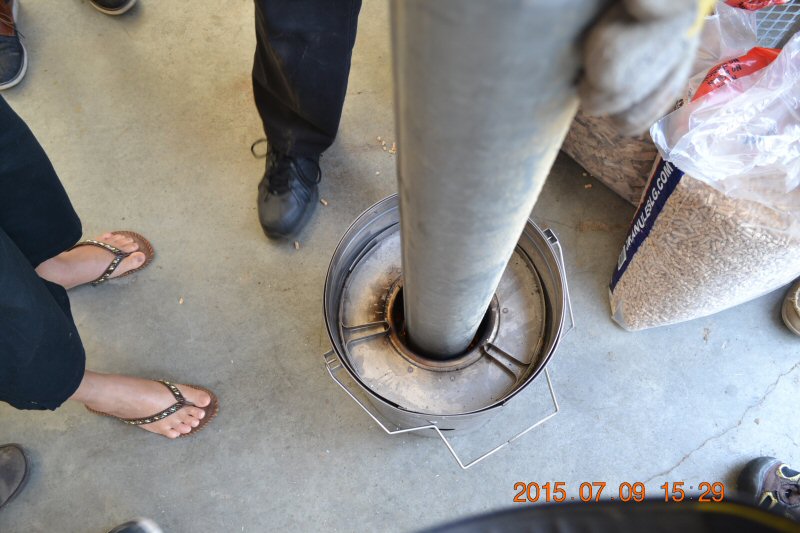
Lighting
another TLUD stove, burning pellets. The 4" pipe is used to accelerate
the draft and help get the pellets lit.
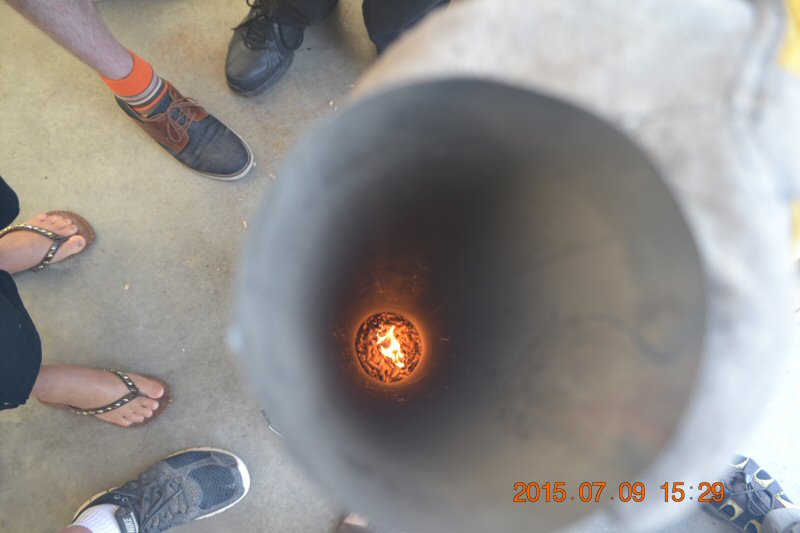
The
bottom of the pipe is touching the pellet bed, drawing air through the
pellets from underneath.
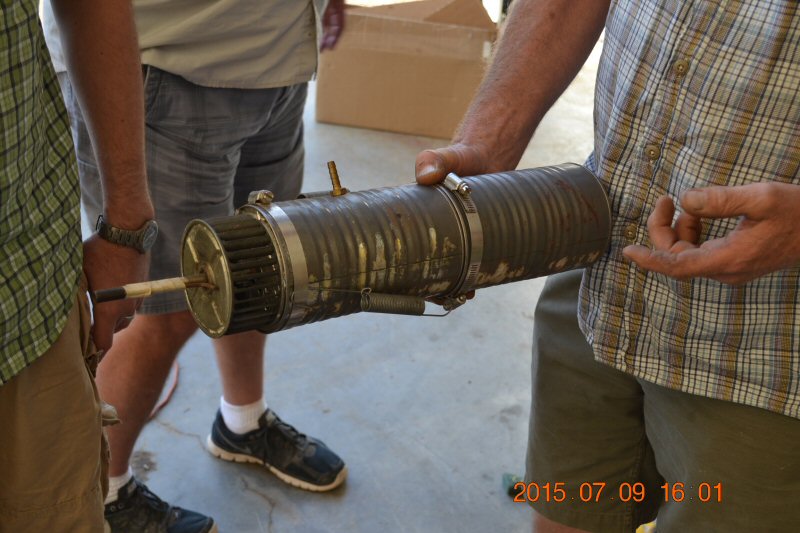
Alex
English shows the Condar portable dilution tunnel that he made many
years ago after a visit to Lopez Labs.
He
has done much innovative research into commercial biomass greenhouse
heating, and has worked closely in the past with
CANMET,
the Canadian government combustion laboratory.
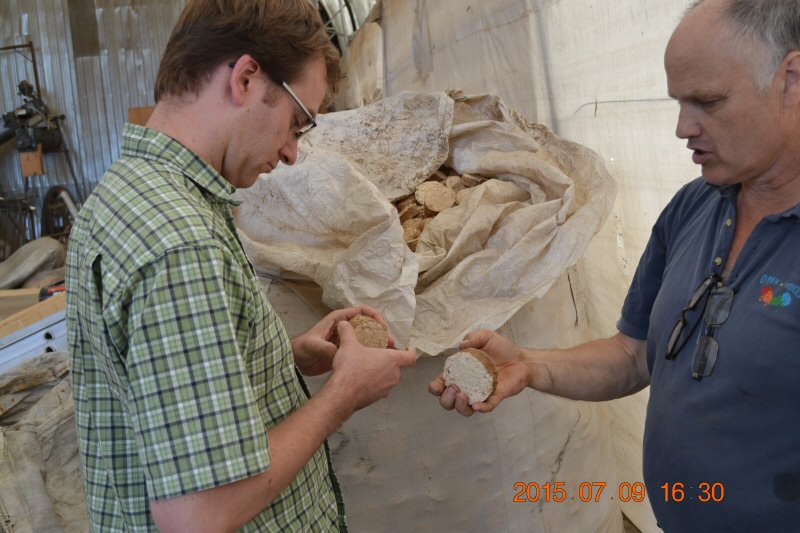
Terrence Sauvé examines densified brickets that Alex has experimented
with. On the right is Brian Burt, the owner
of
the greenhouse operation.
Terrence
is an engineer working for the Ontario Ministry of Agriculture,
consulting on farm scale biomass systems.
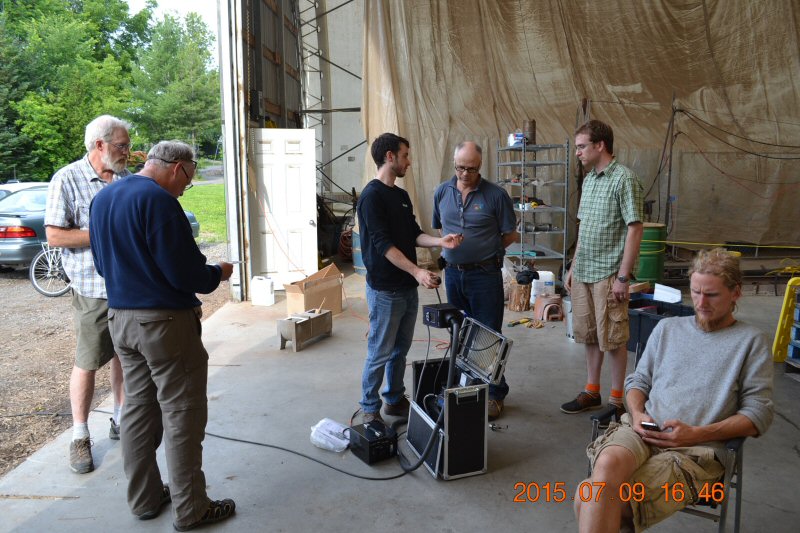
In
the black shirt is Nathan Jones, who is a field engineer for Combined
Heat and Biochar, with ClearStak
He
is demonstrating the Wohler real time particulate emissions analyzer.
Second from the left is Julien Winter, a soil scientist who is involved in a biochar project in Bangladesh.
Julien prepared this
summary of his recent TLUD research.
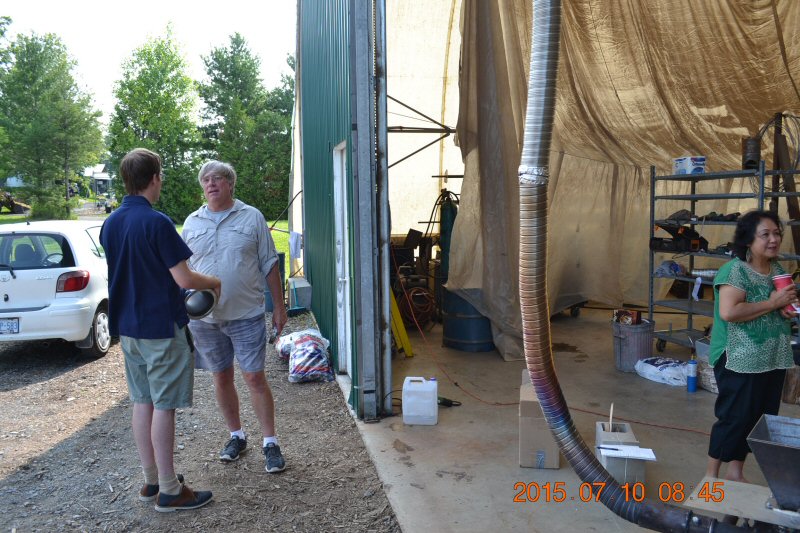
Terrence Sauvé chats with Lance Grace, who is an aeronautical engineer and the
principal at Clear
Skies Unlimited
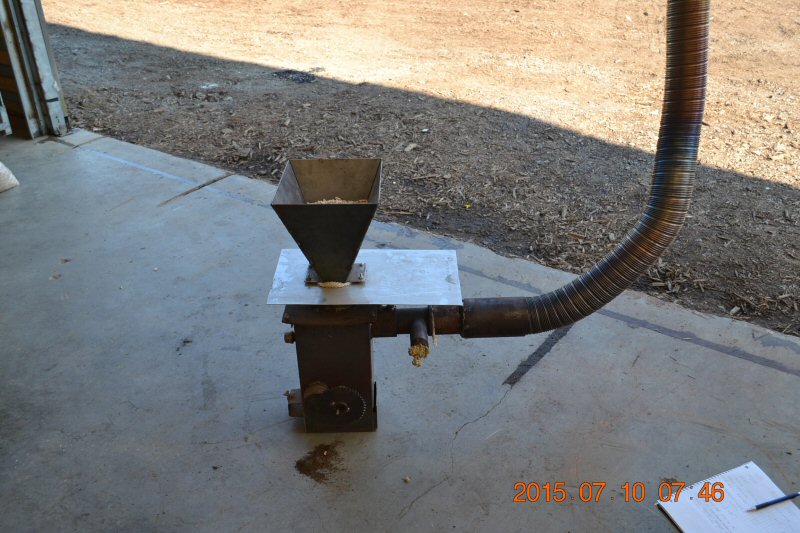
This
is an experimental gravity feed pellet stove that Alex English built,
and hooked up for a demo.
It
needs no electricity. The sprocket in the front is connected to a
manually operated shaker grate.
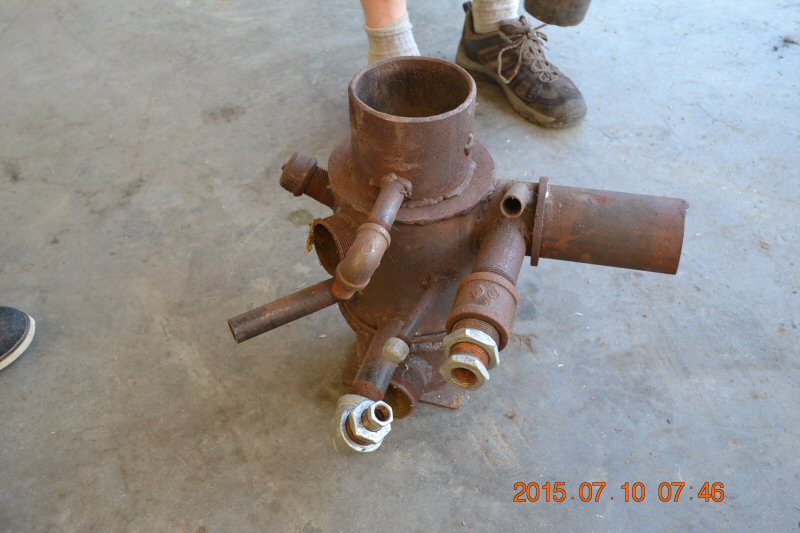
This
is another prototype without a shaker grate.
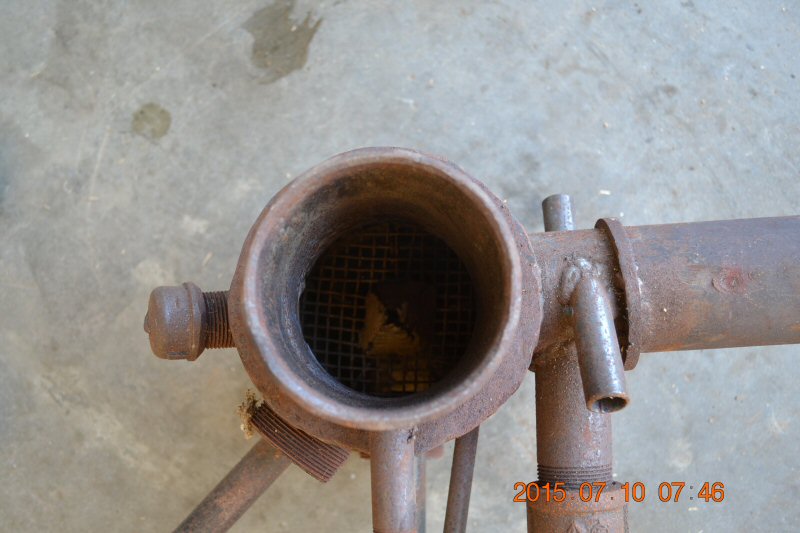
Notice
the pyramid at the center of the mesh grate, with an air outlet in the
center. It is designed to prevent ash clogging from the
pellets.
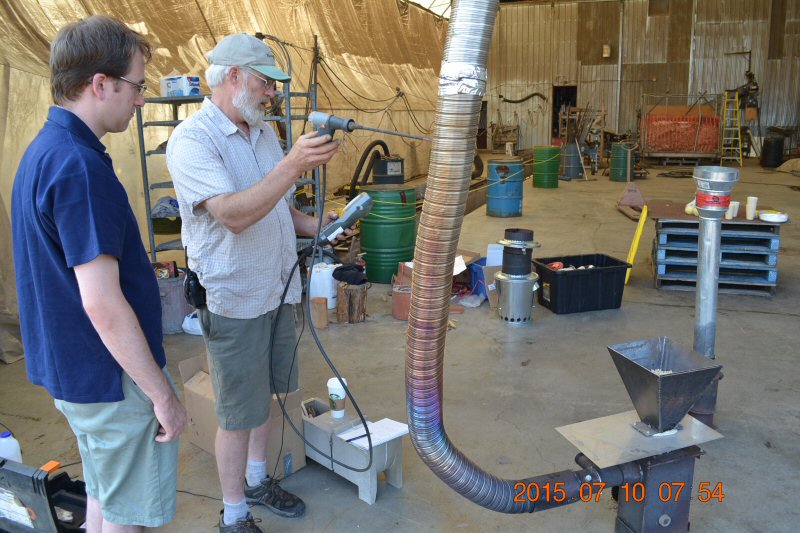
Checking
the combustion with a Testo. It was very clean, with very low CO.
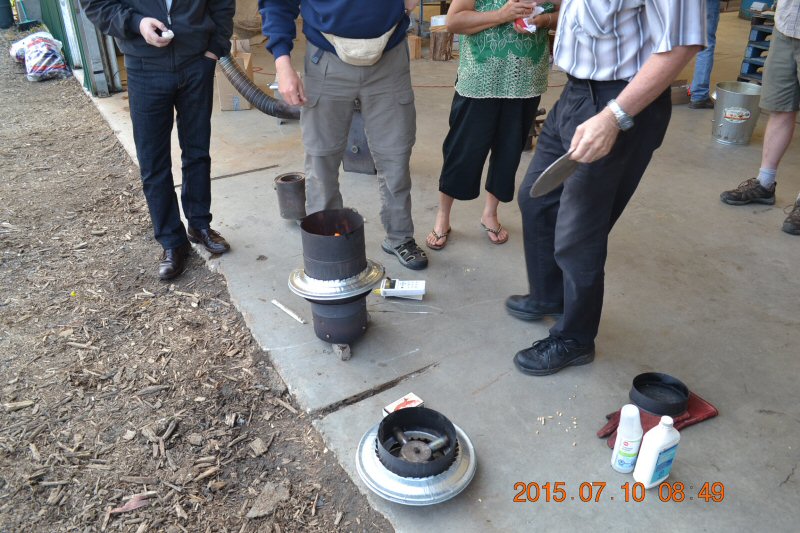
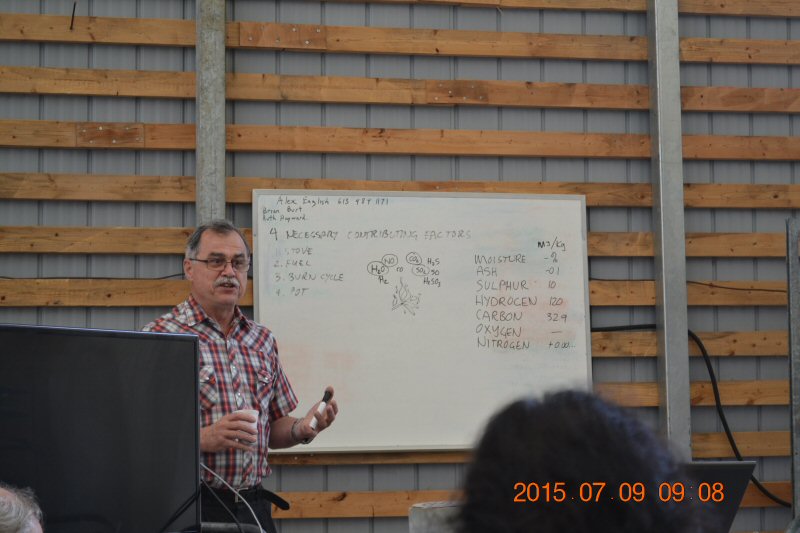
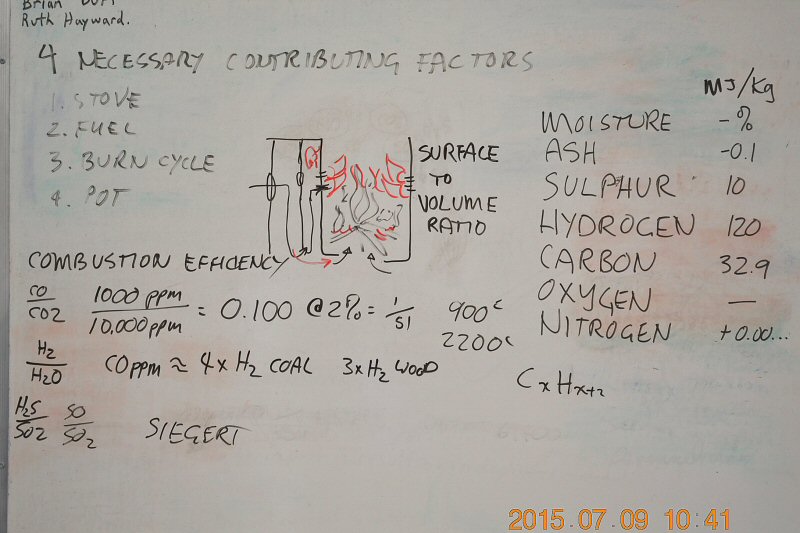
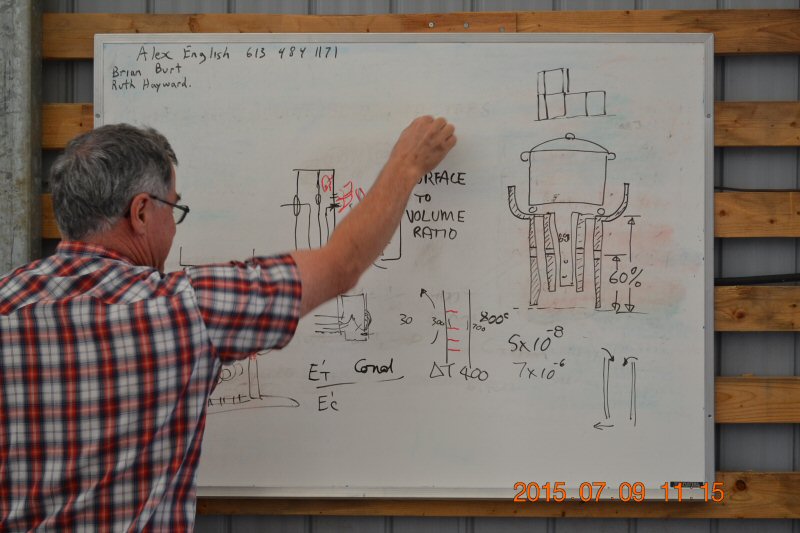
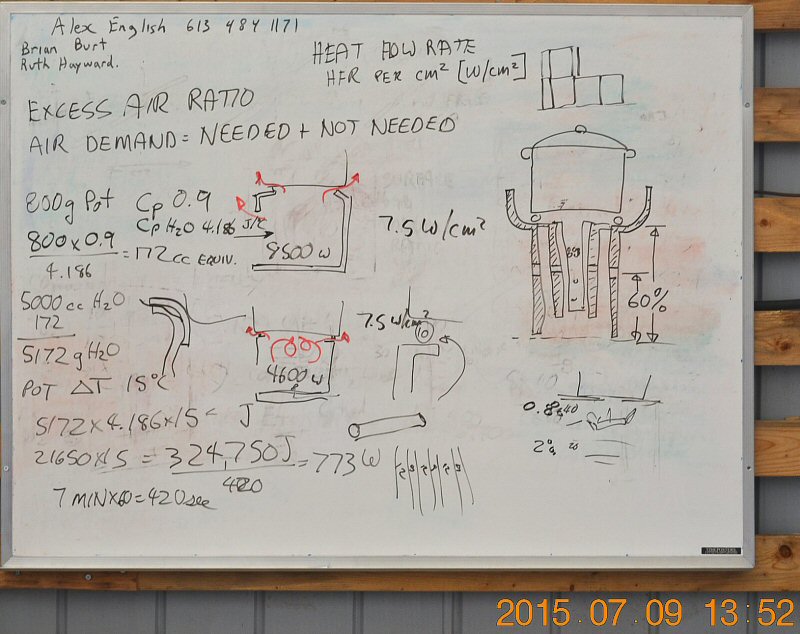
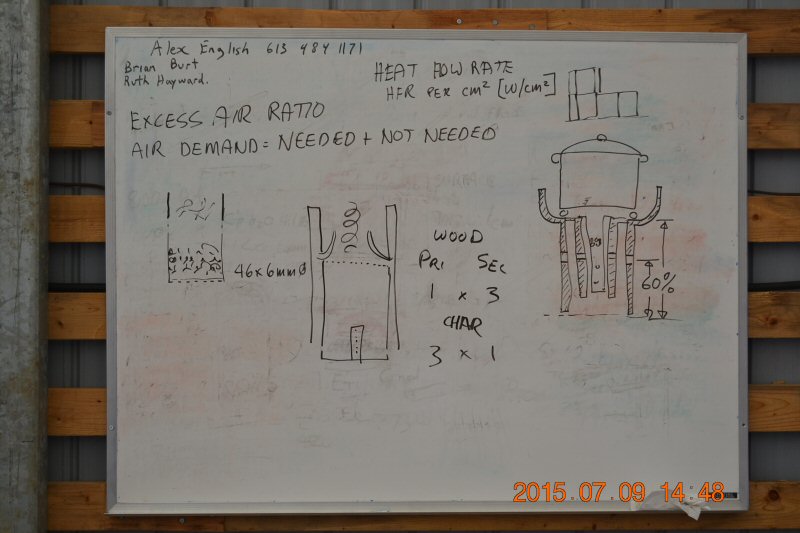
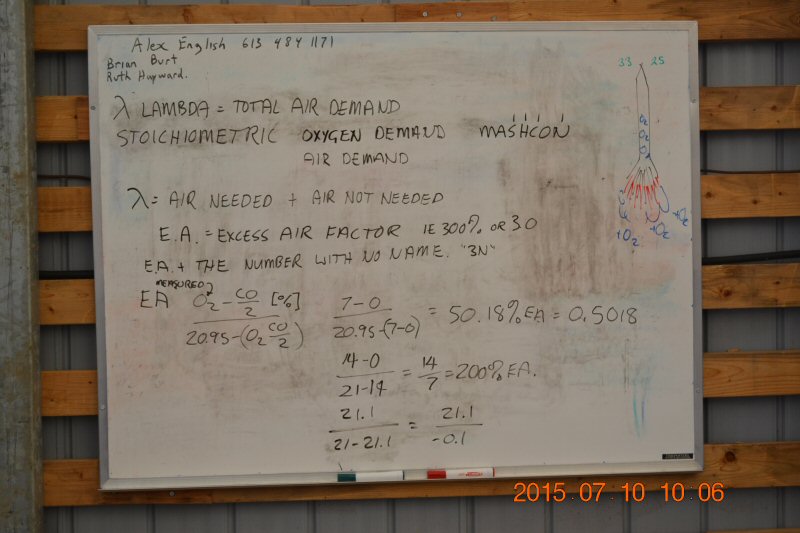
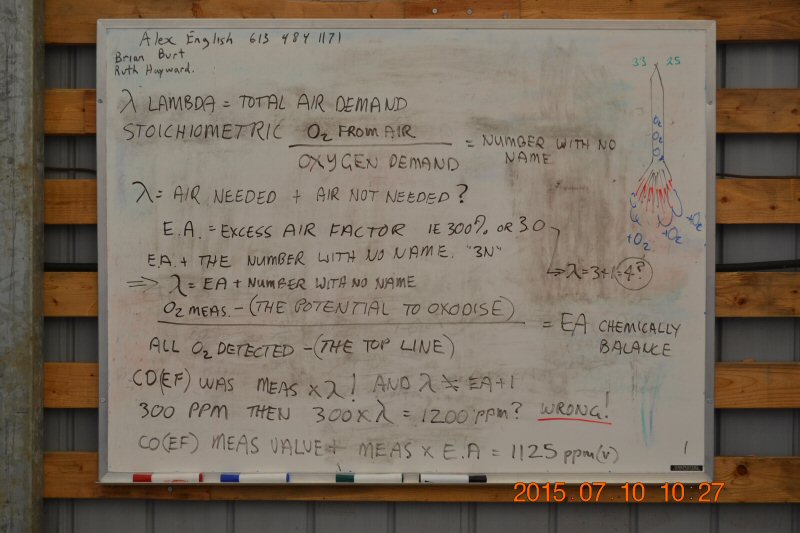
Crispin
presented results for the first time from very recent research, indicating
significant error in how
emission analyzers have calculated excess
air ratios up to now, which induces corresponding errors in reported
emissions and efficiency calculations.
Wood
is 40% oxygen, and since this is much higher compared to other fuels, and has no
associated nitrogen, this is can be
a significant source of error when
using conventional excess air calculations intended for other fuels at steady state.
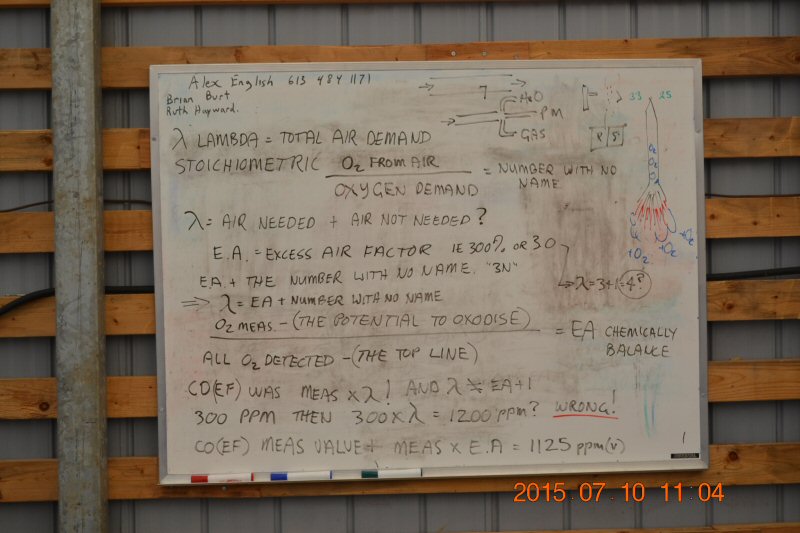
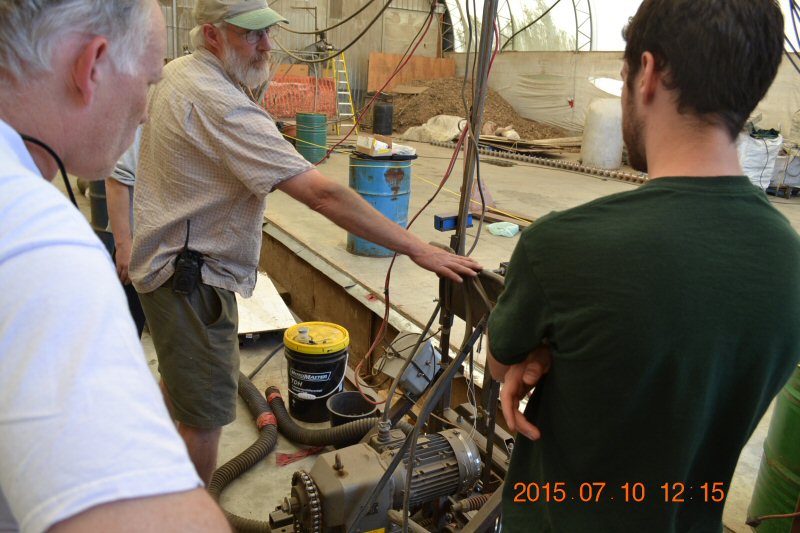
Alex
gave us a tour of his chip burning operation. This building is normally
filled with fuel, and he is showing us the automated
fuel
conveyor system that he developed and built. An auger has sensors that
allow it to detect where the fuel pile is, and orient itself
to
convey chips to a conveyor trough.
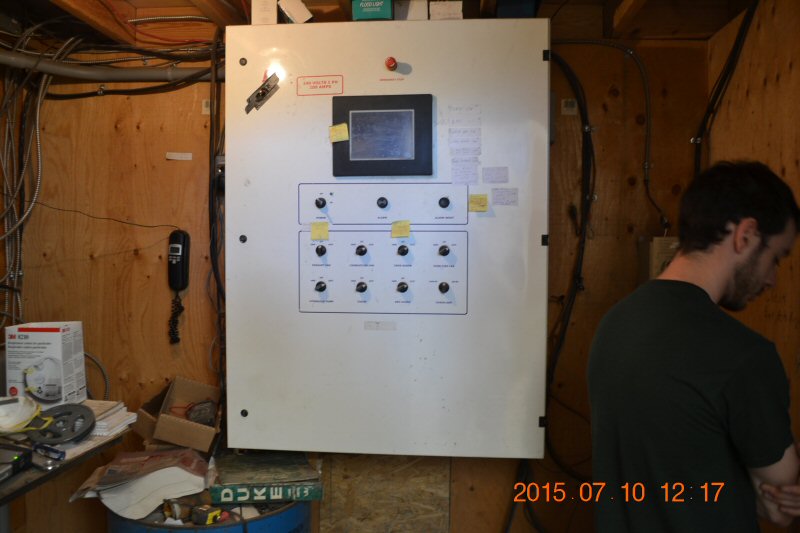
The
PLC control system for the boiler.
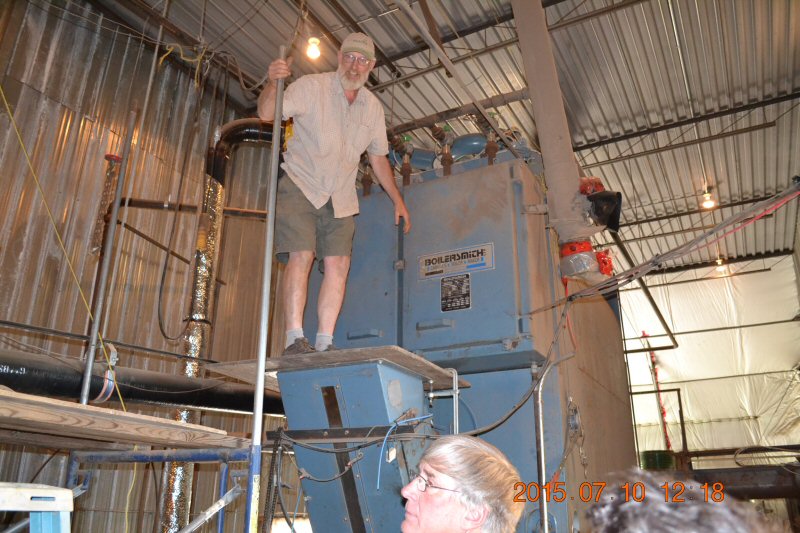
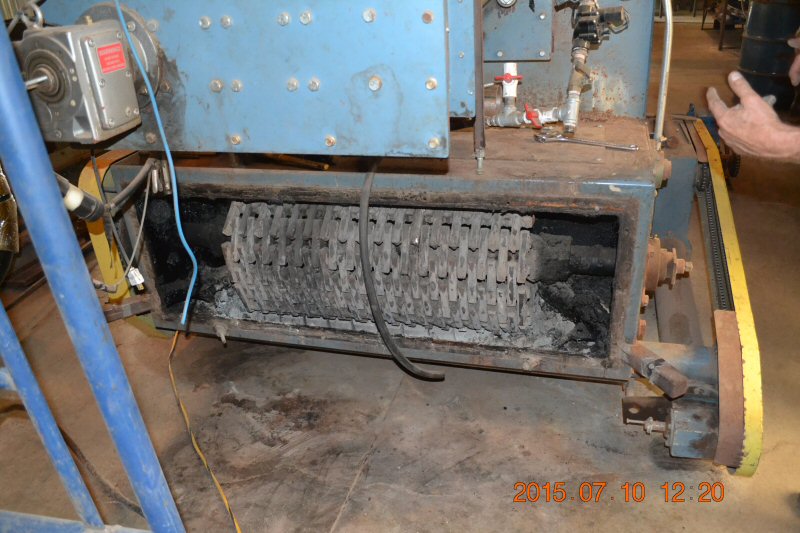
The
moving chain grate.
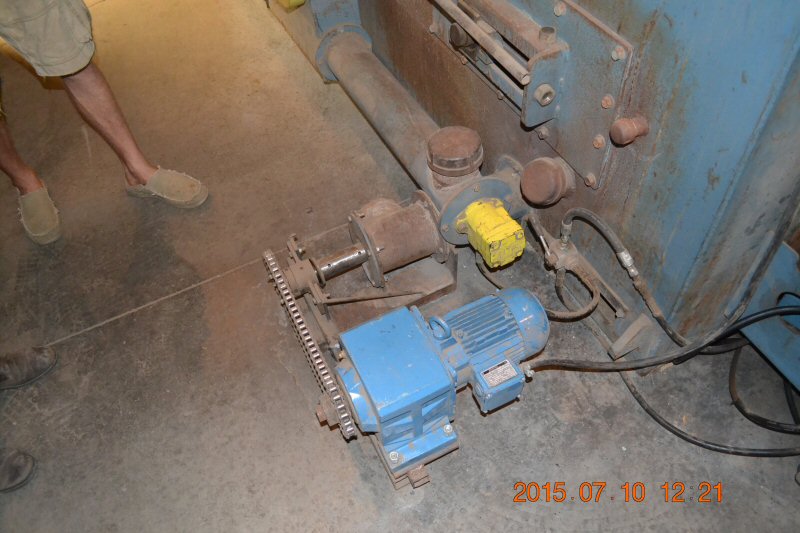
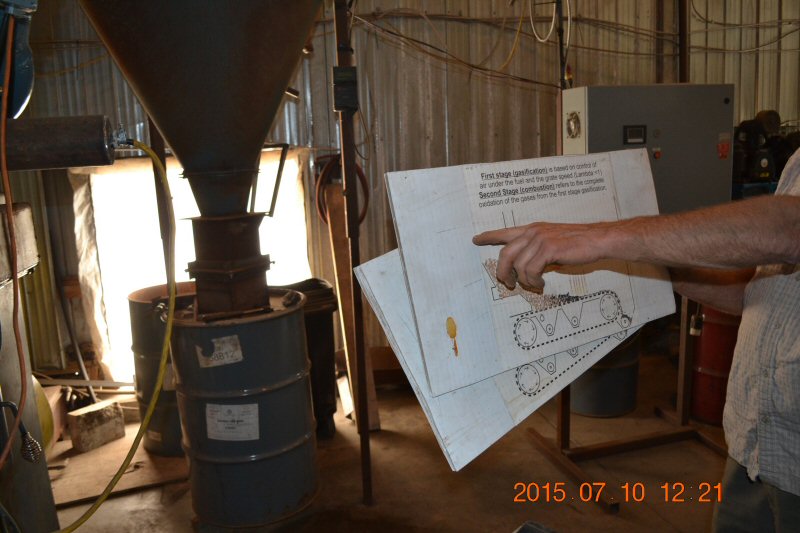
The
boiler can be used to make biochar, by closing the primary air supply.
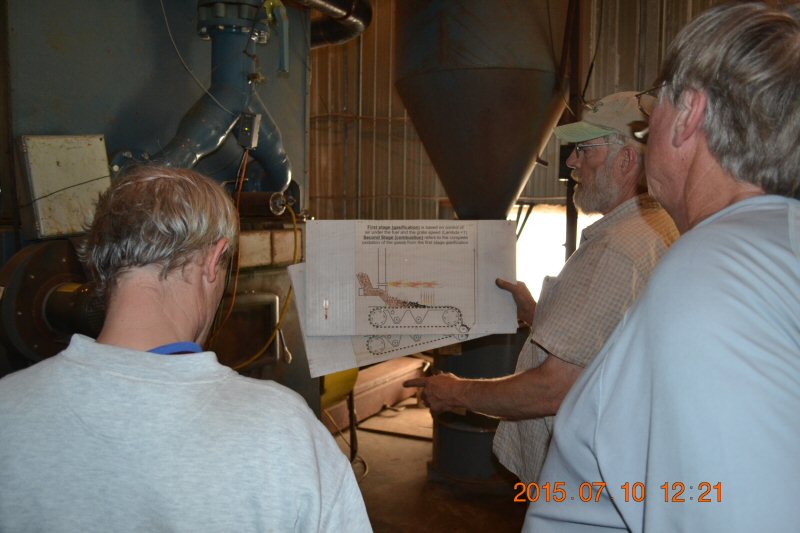
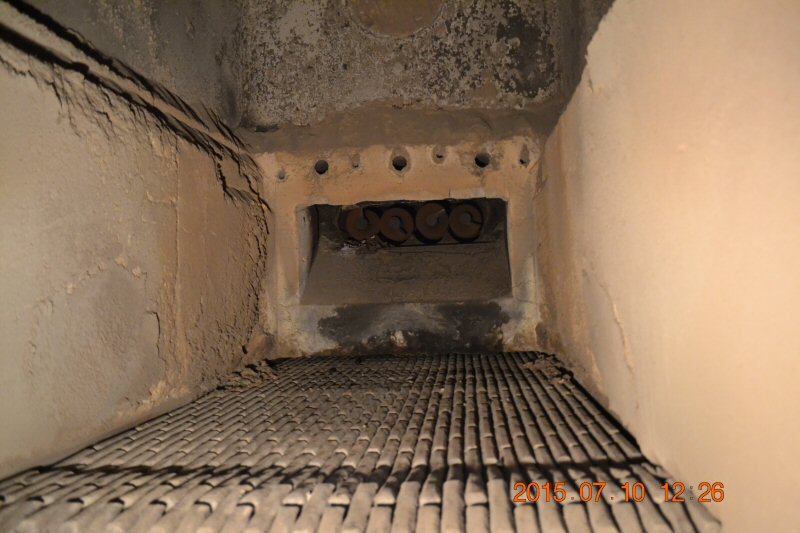
Four
auger at the end are ganged in opposite directions, and feed the chips
into the fire chamber.
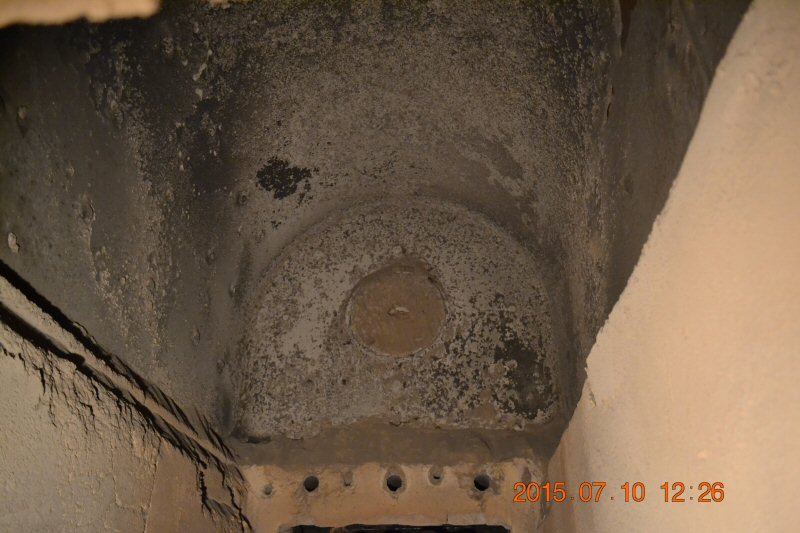
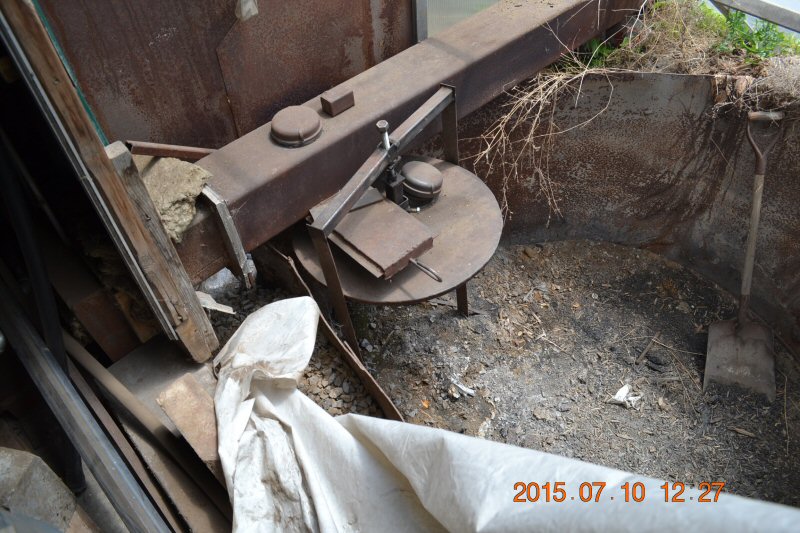
A
prototype biochar takeoff. The square duct contains an airtight auger,
that drops off the biochar into a drum.
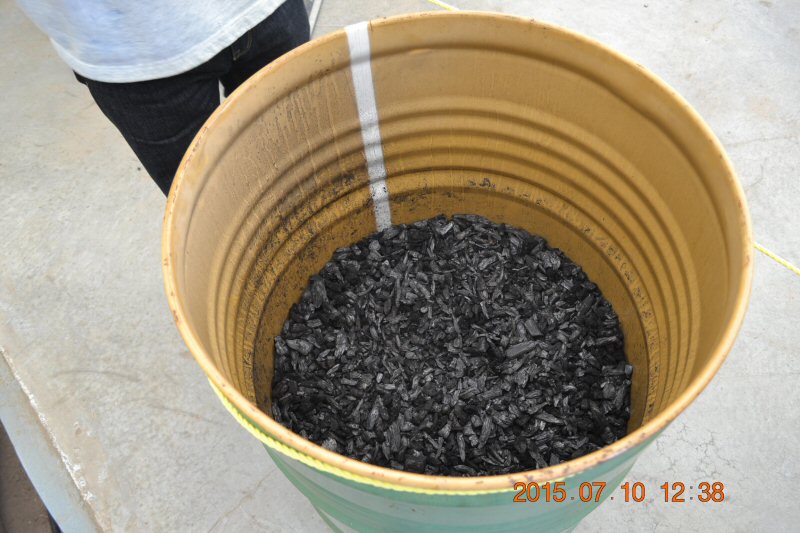
Biochar
in a drum.
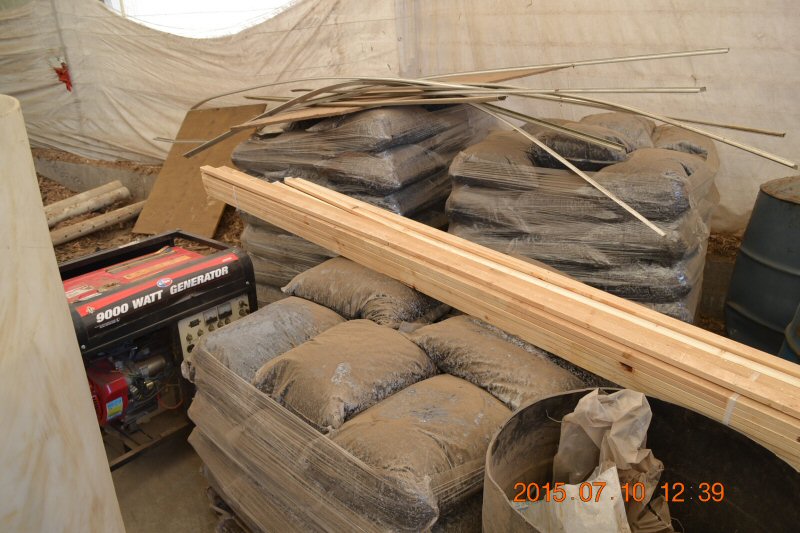
Bagged
biochar.
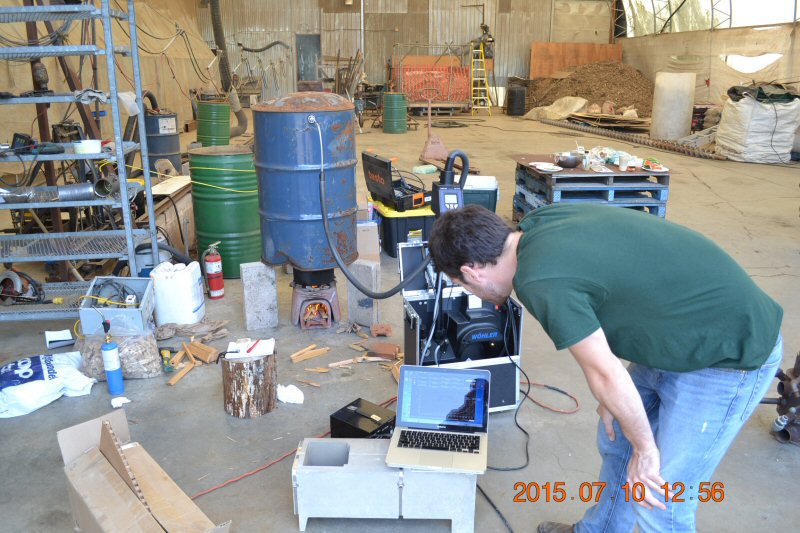
One
of the participants, Rebecca Vermeer, is originally from Indonesia and
does stove work
there. Here we have her clay stove
set up underneath an improvised
hood using a steel drum. Note the hose from the Wohler sampler to the
blue drum hood.
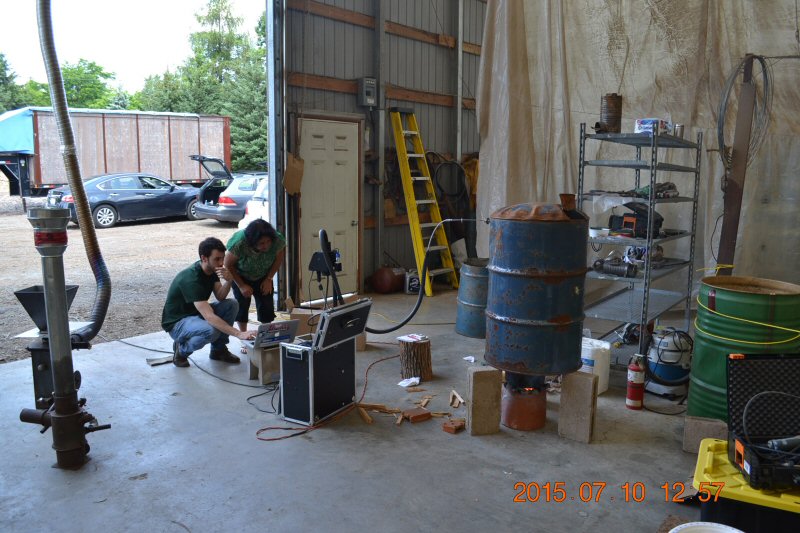
Rebecca and Nathan watch the real time data on her stove.
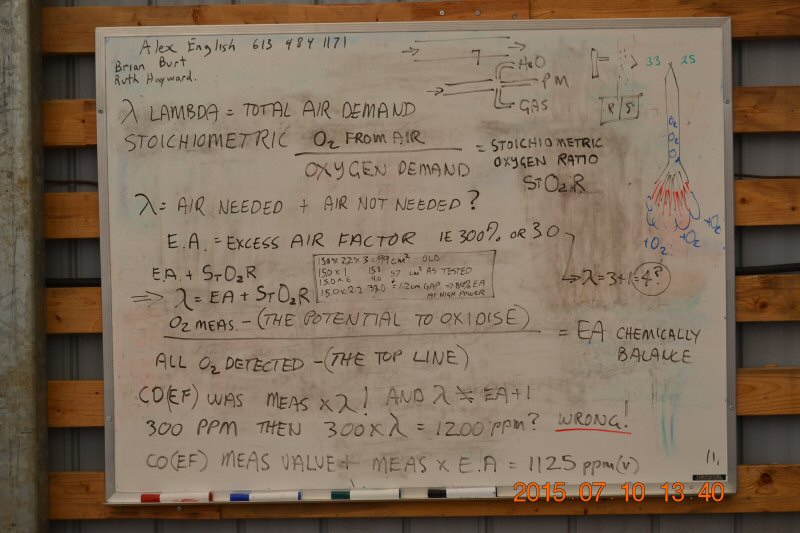
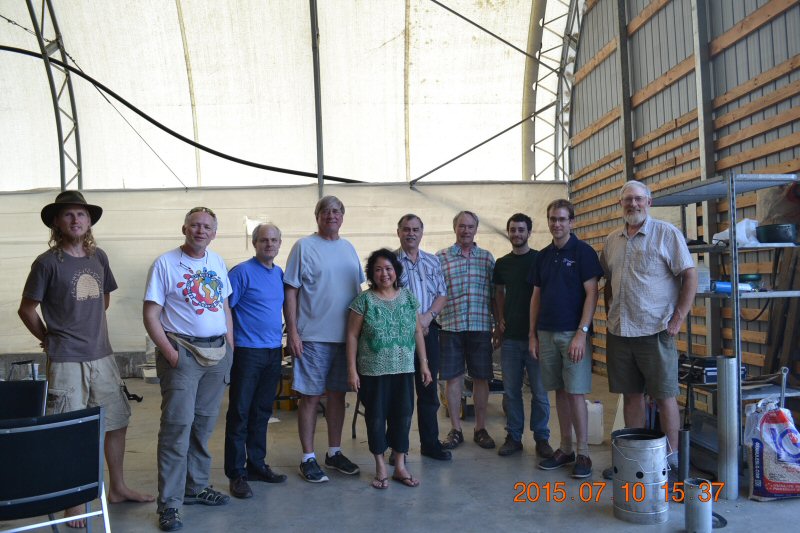
This
page was last updated on October 4, 2016
This page was created on July 11, 2015
Back
to:
