
2015 MHA Annual Meeting
Batch fired Rocket Bell
with Peter van den Berg
Back to Wildacres 2015 Photo Report

View down the top of the riser. Exit from firebox and entry into riser is at top.
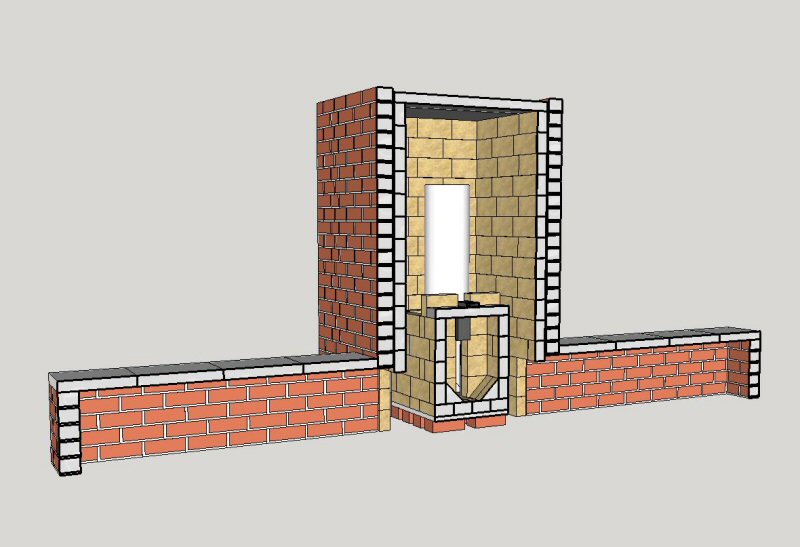
Section through heater.
Download the open source Sketchup model
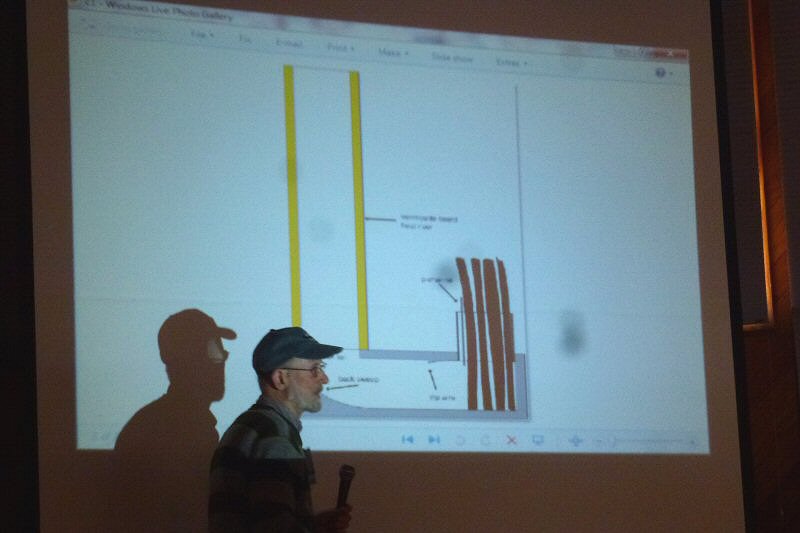
Peter gave a presentation at the annual meeting, prior to his hands on workshop.
He has done much leading edge research on a batch burning rocket bell design.
You can find the graphics files for Peter's MHA seminar here:
Follow some of the current progress on the rocket stove forum, where Peter often hangs out.
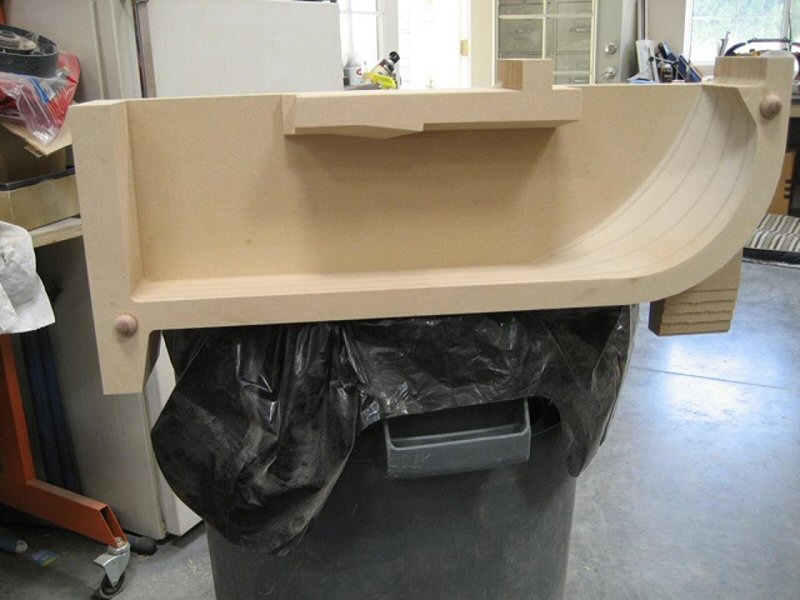
A combustion tunnel featuring surface details to break up laminar flow and initiate turbulence.
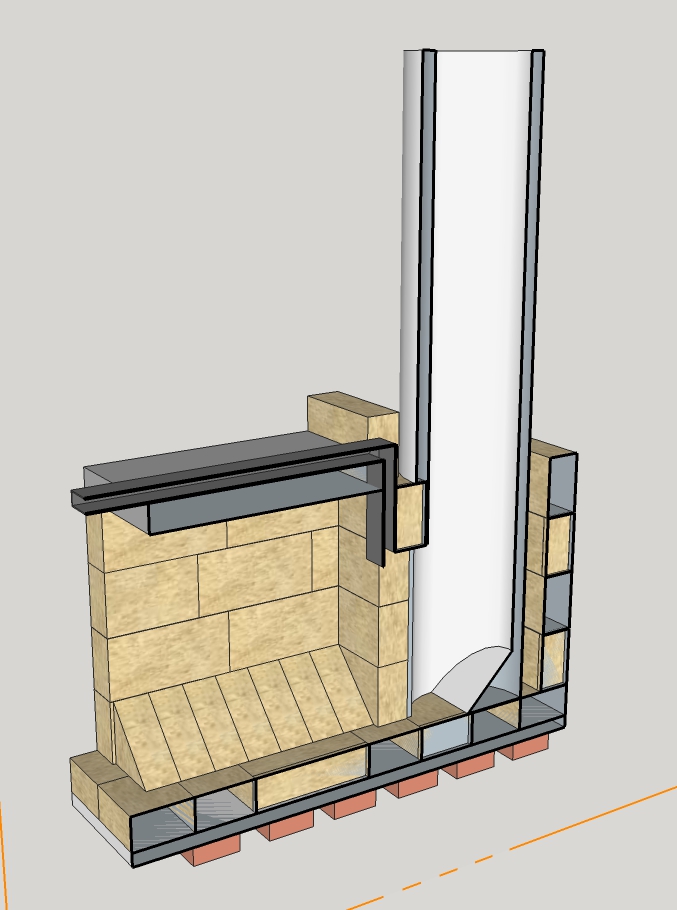
Detail of the current P tube design that injects air at the exit slot of the firebox.
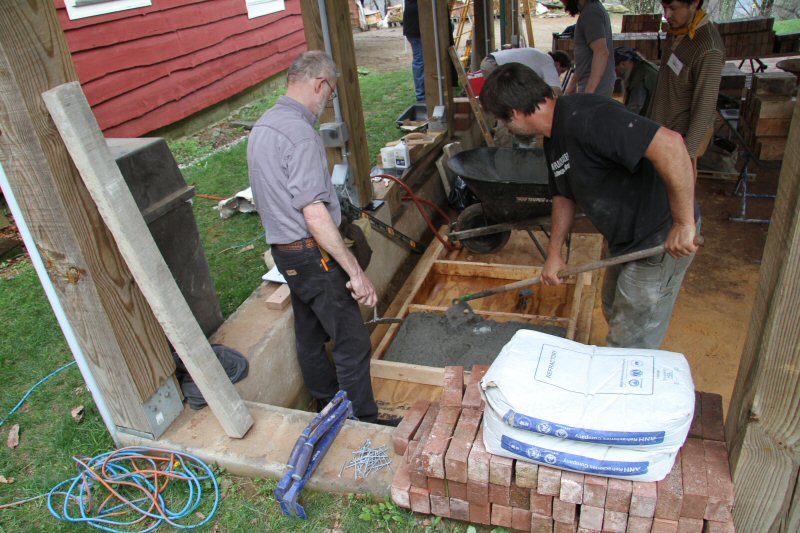
Casting ceiling slabs from castable refractory.
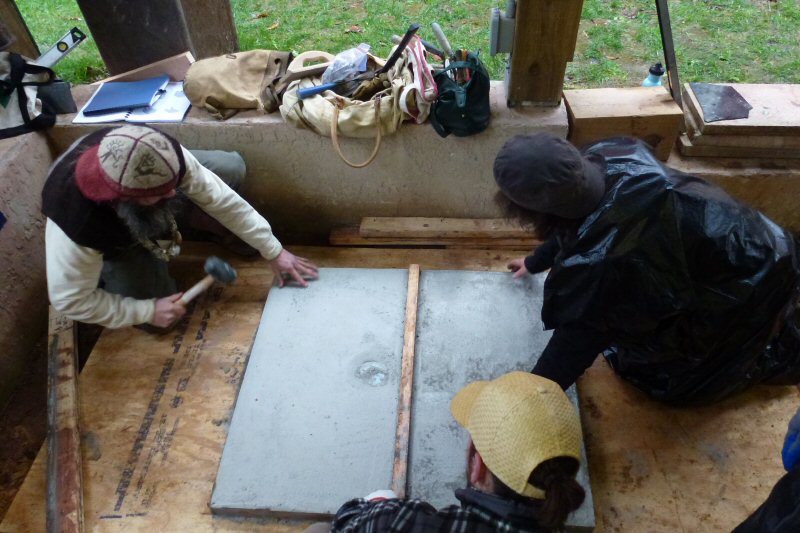
Demolding the slabs.
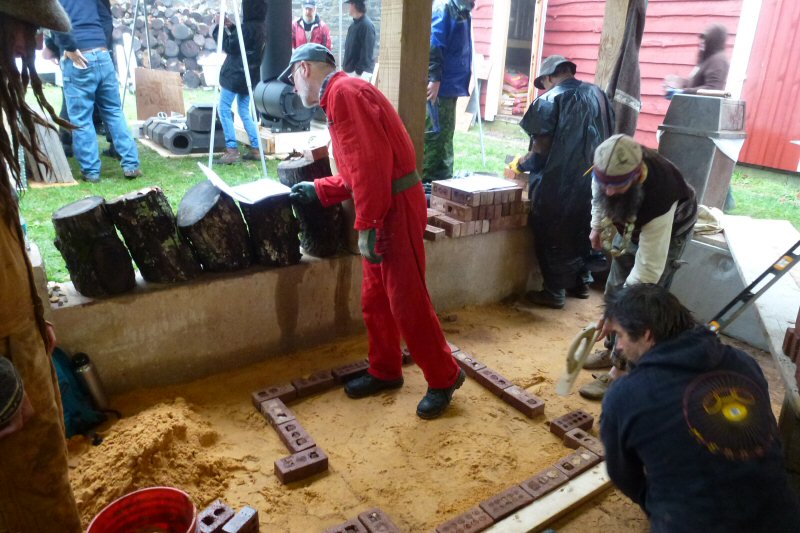
Layout
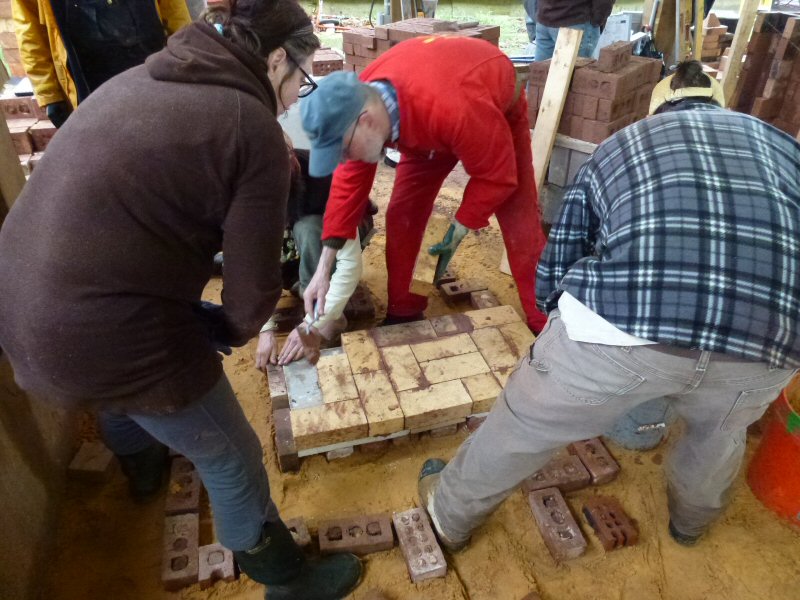
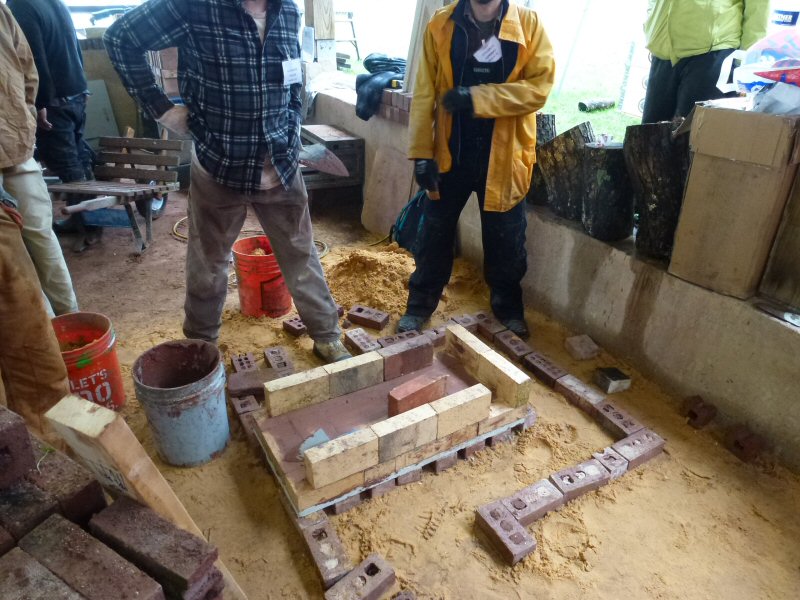
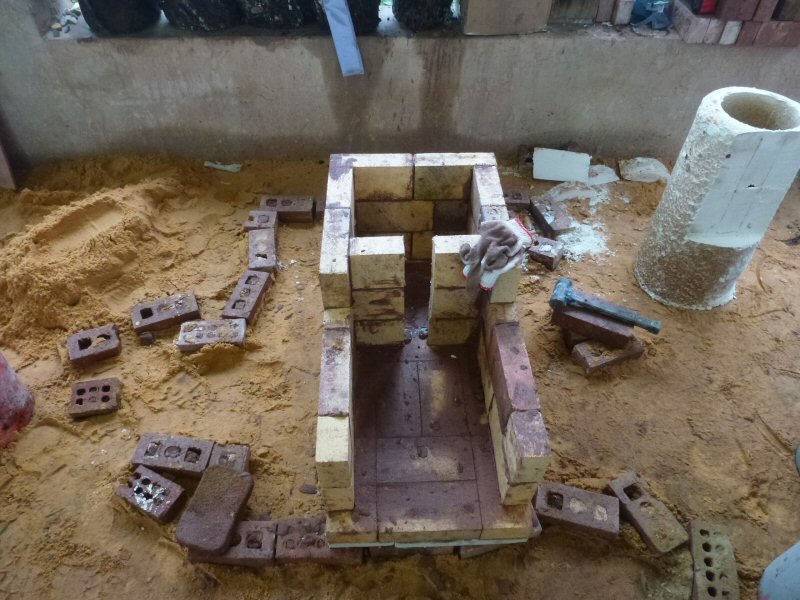
Firebox, with the exit slot to the rear.
Insulated riser tube can be seen on the right. It is made from rigidized ceramic fiber.
Note that it has been notched on one side.
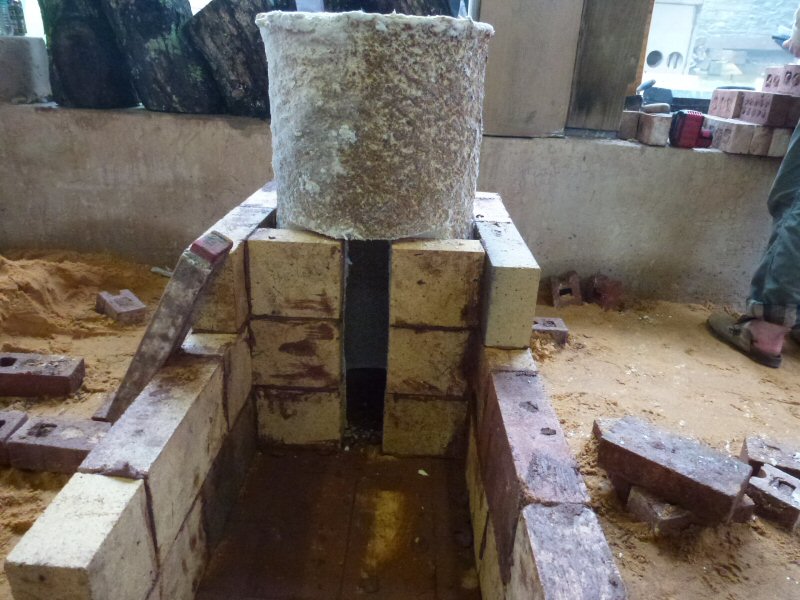
Riser in place.
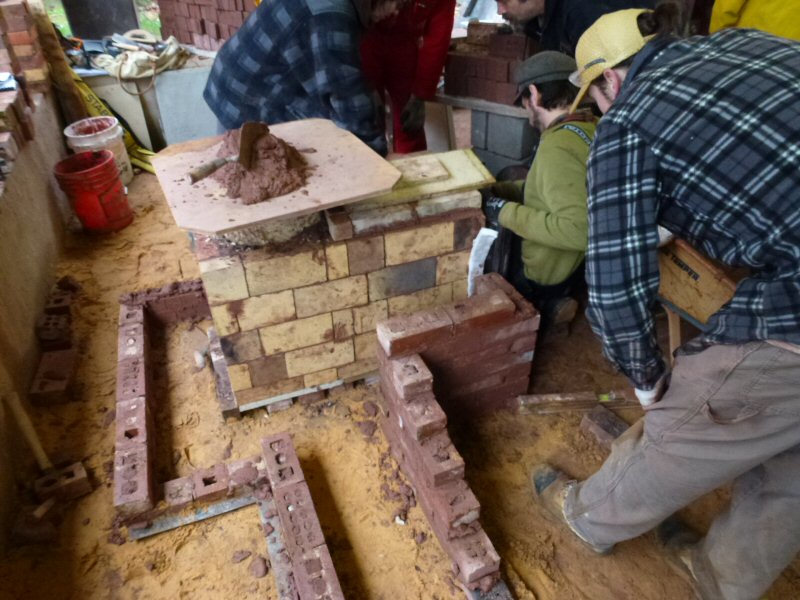
Blind heated benches. They work on the bell principle, also known as buoyancy or Bernouilli's principle.
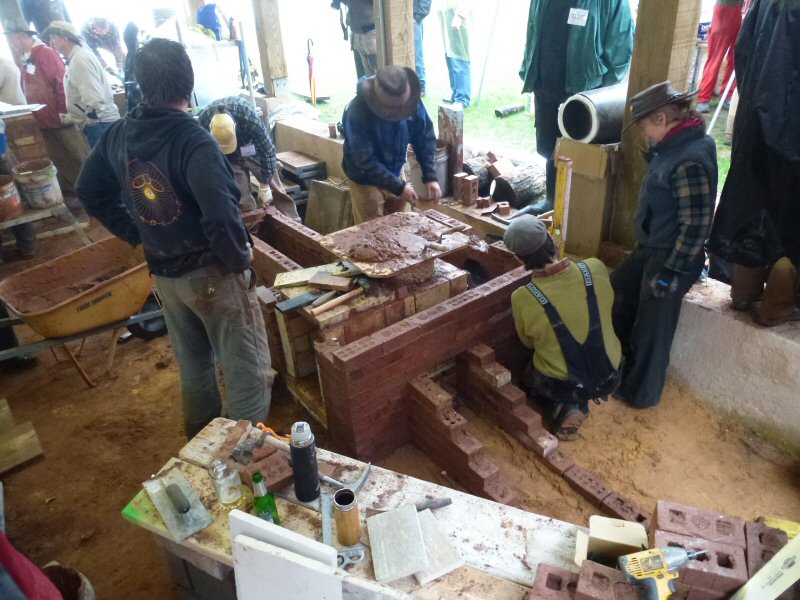
Chimney exit is visible just behind the riser chamber.
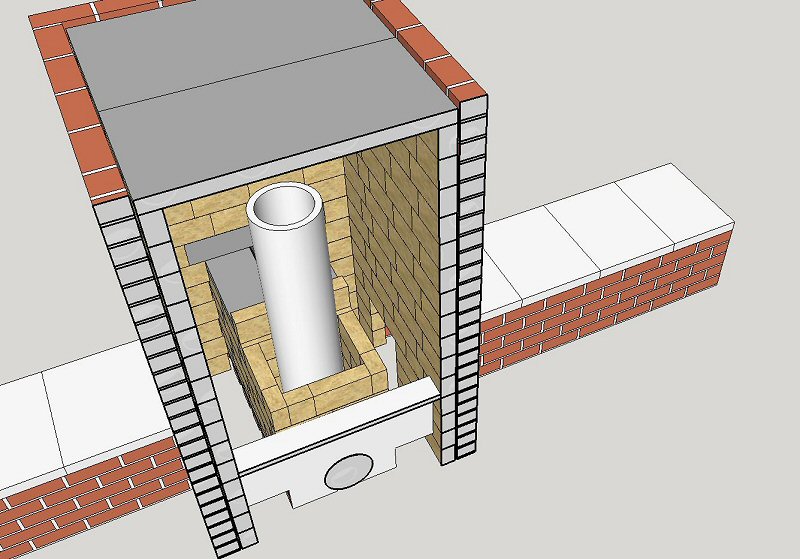
Section, viewed from the rear.
The calcium plate divider is there to keep
the exhaust openings symmetrical and as low as the bottom half
of the bench.
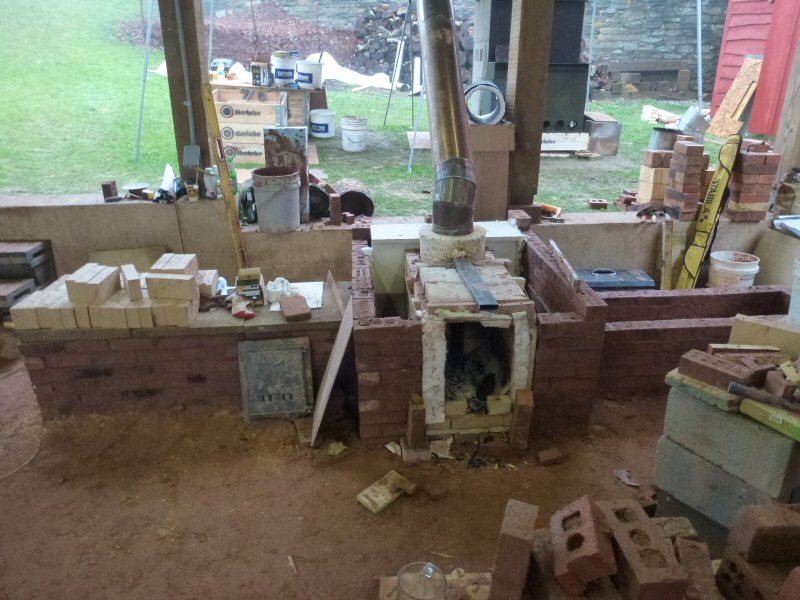
The 1"x4" steel tube P-channel is visible on top of the firebox ceiling. It supplies air to the top of the firebox exit slot.
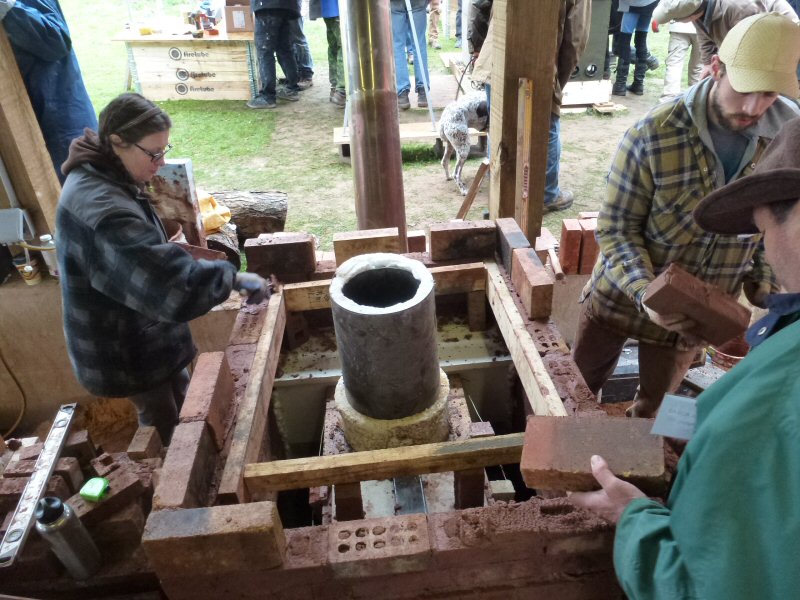
An extension is added to the riser. It is site fabricated from two pieces of stainless pipe and ceramic fiber.
It would not be suitable for long term use.
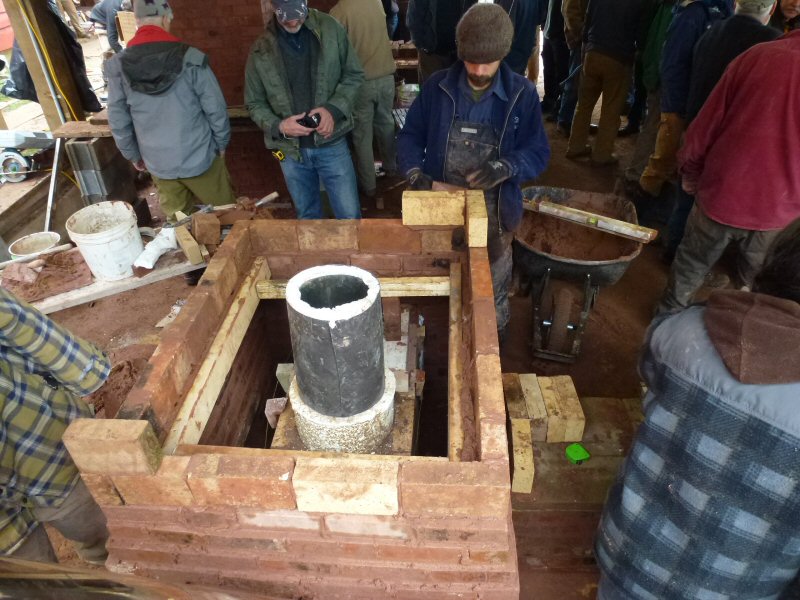
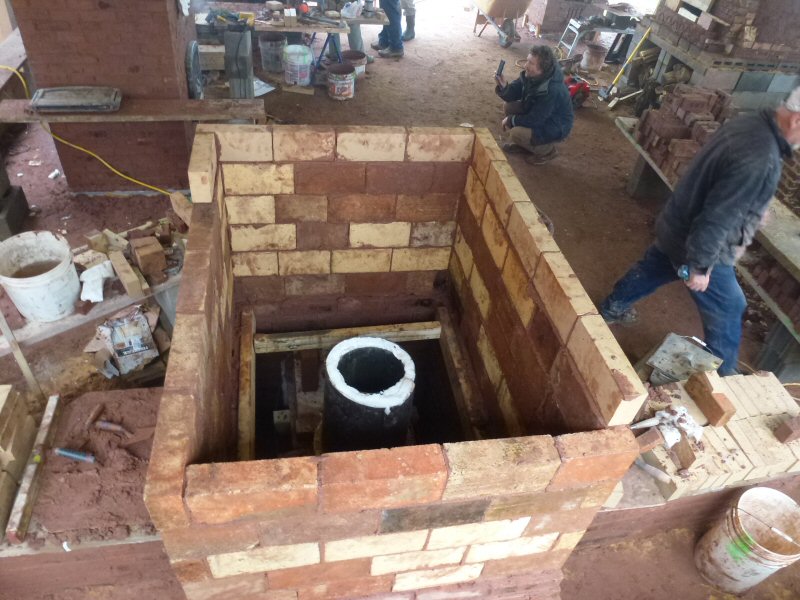
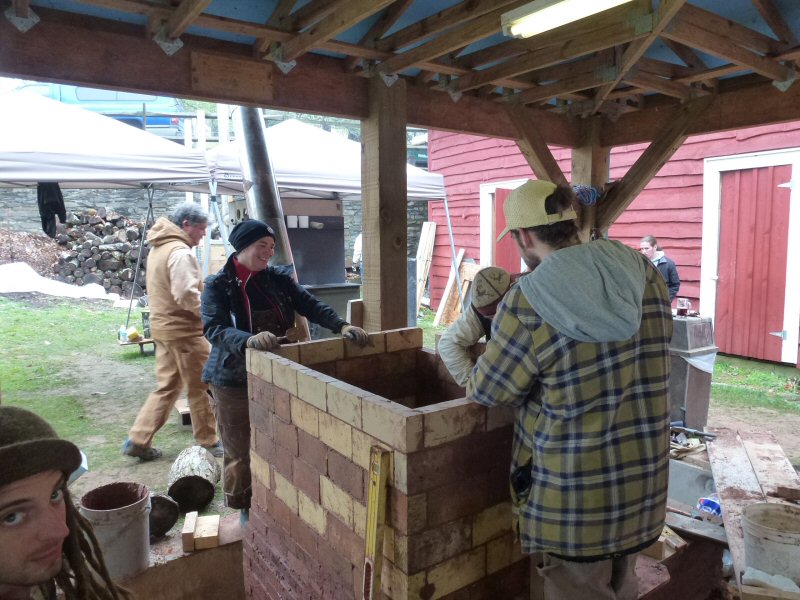
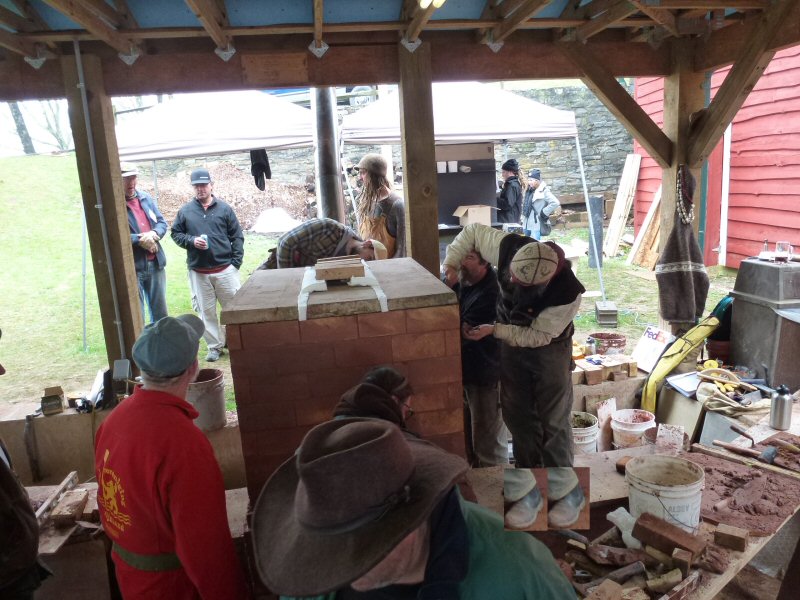
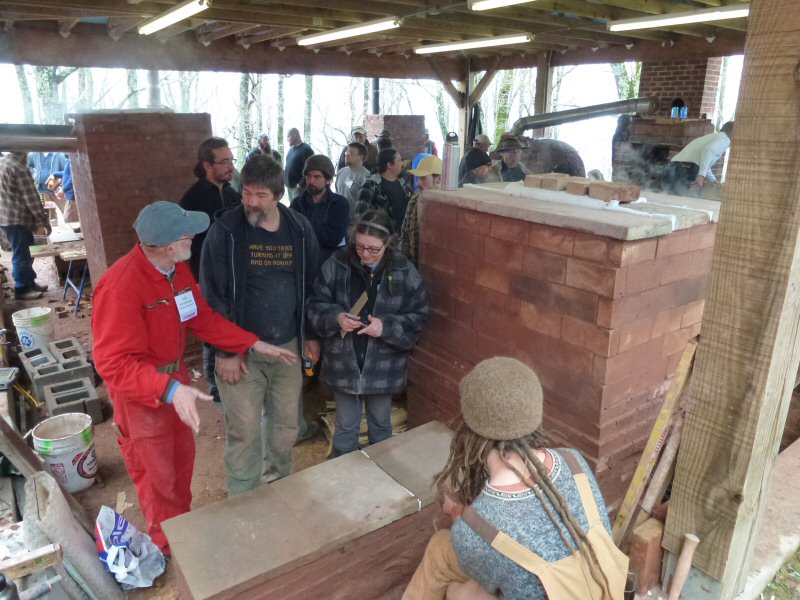
Ceiling slabs and bench top slabs in place.
Heater is being fired to dry it out.
You can observe the warming of the benches by the lighter dry patches on the bench tops.
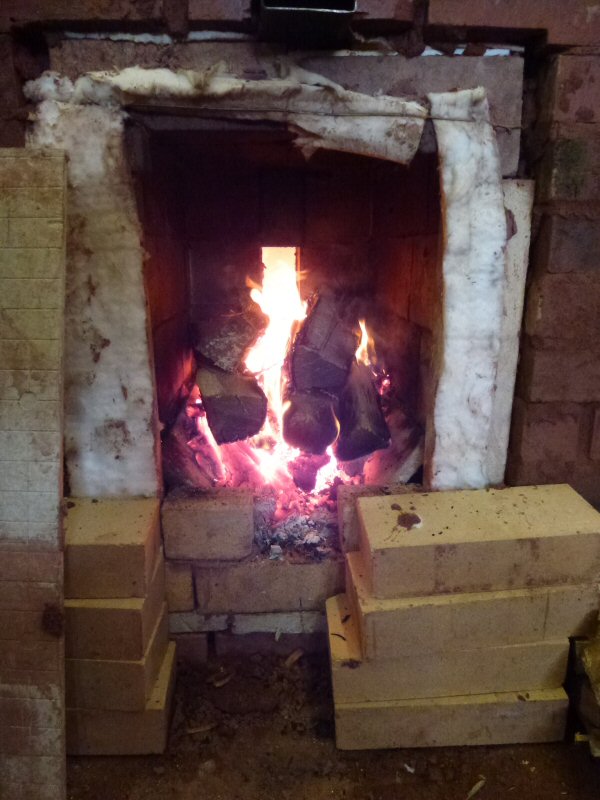
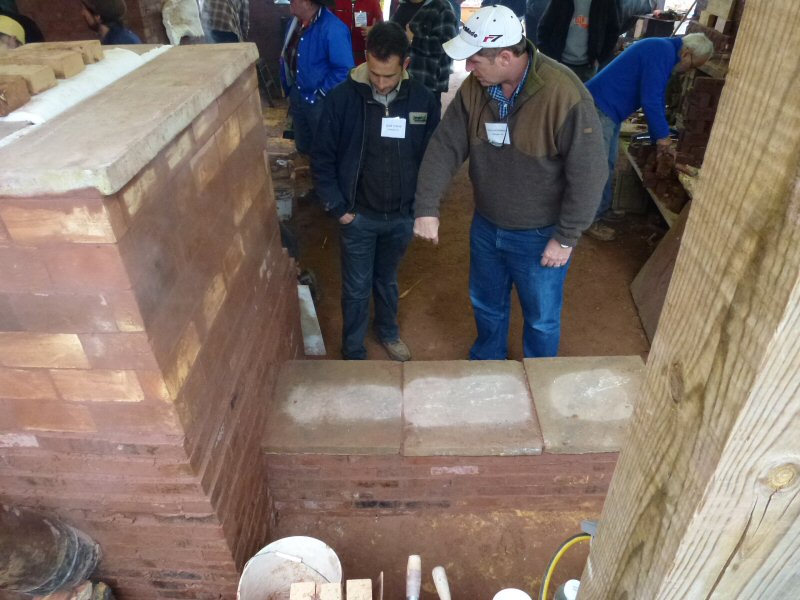
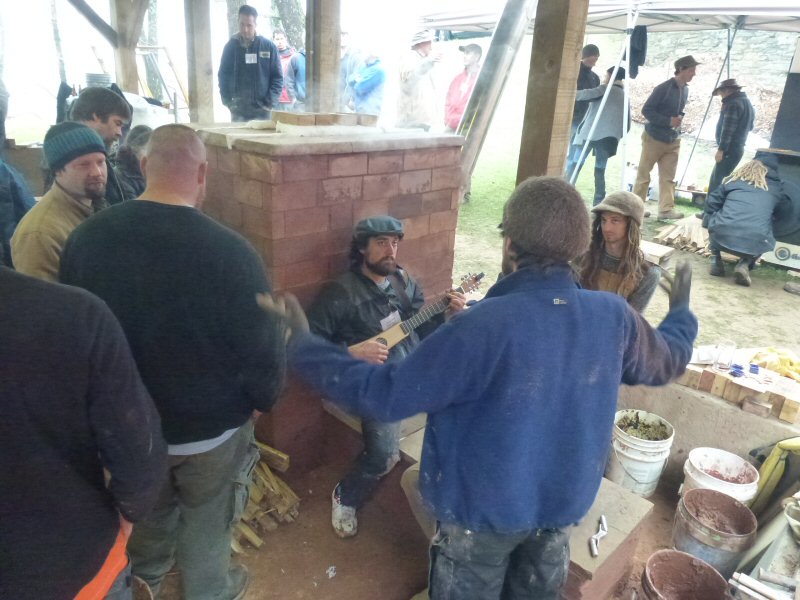
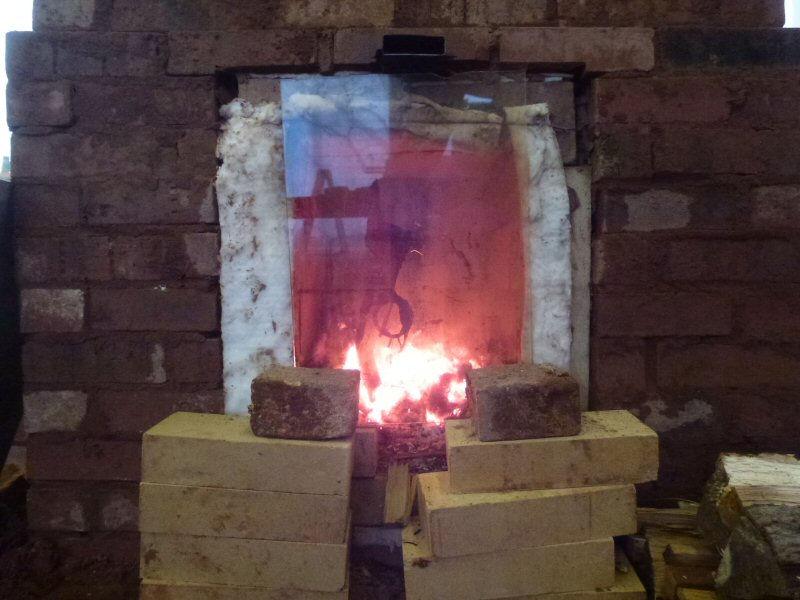
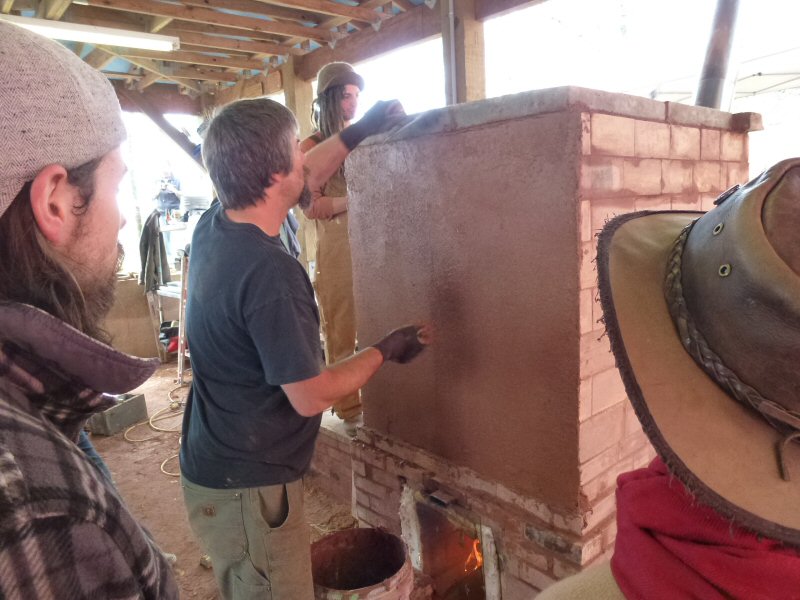
The next day, the top slabs were removed, and the bell was raised two courses (9").
The added heat
exchange, in Peter's opinion, reduced draft enough to tip the
system out of clean burning mode just
now and then. Temperature of the
exhaust gases was low enough so that one would be able to hug the
bare stovepipe.
Eric Moshier had brought an additional Testo
330-2, and the burn on the second day seemed to have higher CO.
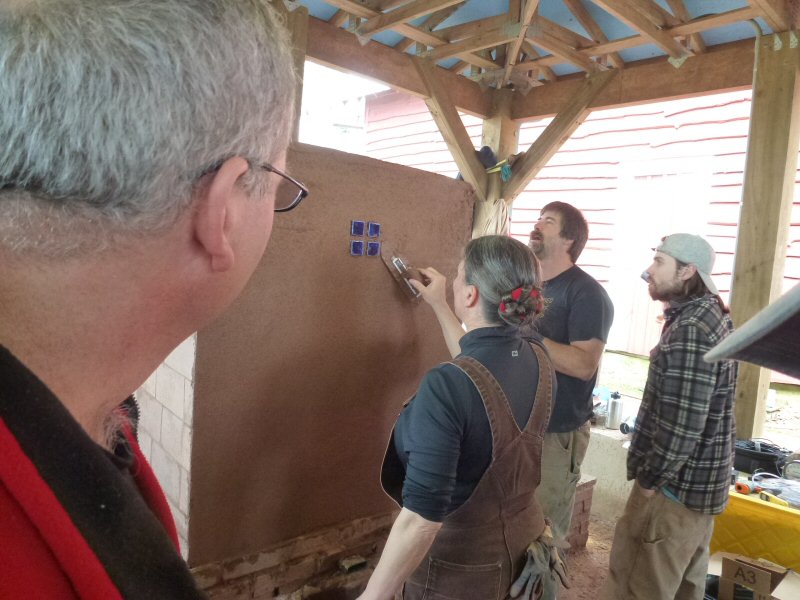
Kirk Mobert, second from right, made earth plaster out of the
mortar clay and sand plus local horse manure from the
adjacent
paddock. The plaster was added when the stove heated up and
finished with some finer local clay with a lot
of mica in it.
Thickness of the whole layer was just 1/4" but the plastered area
didn't show any cracks even when the
single skin heater became too
hot to touch. Thanks to the excellent heat distribution of the
bell and the fibres of the manure.
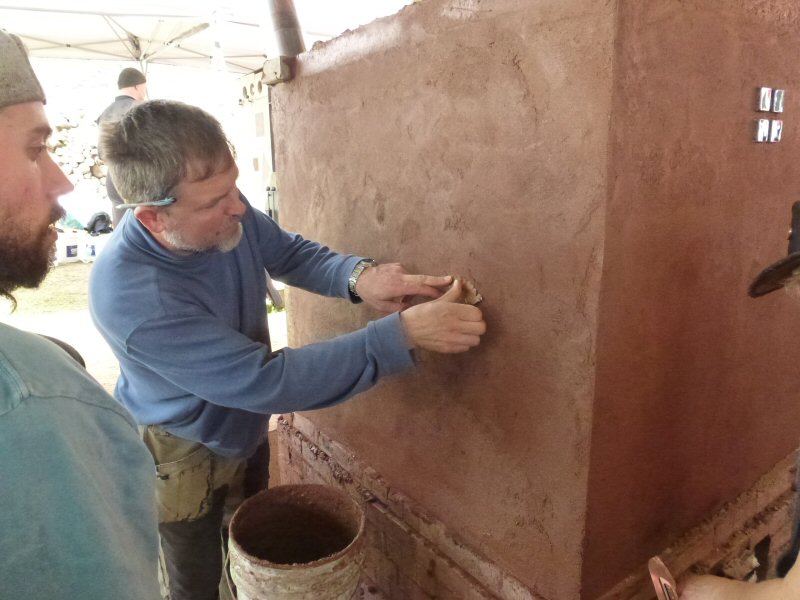
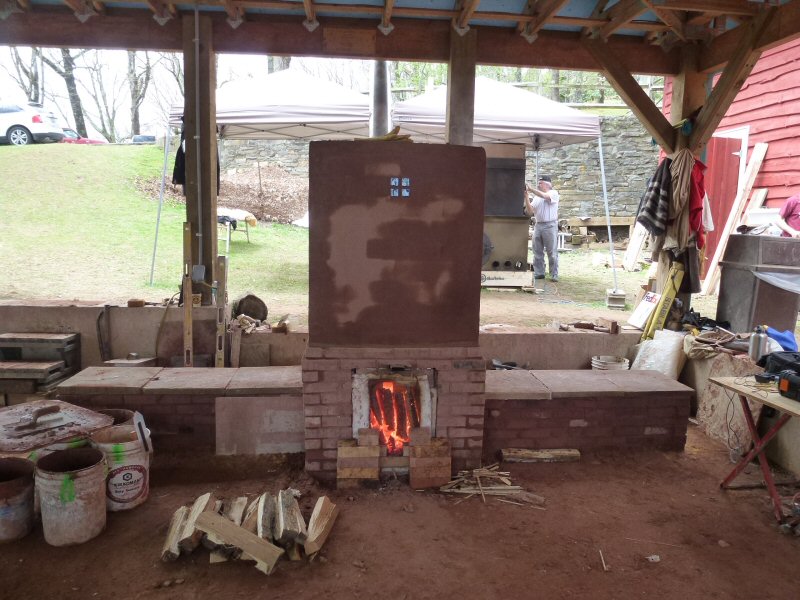
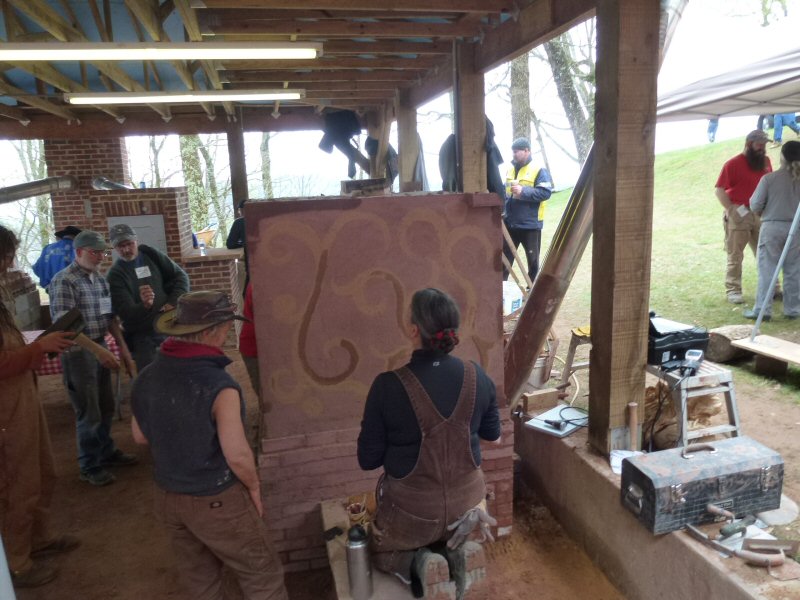
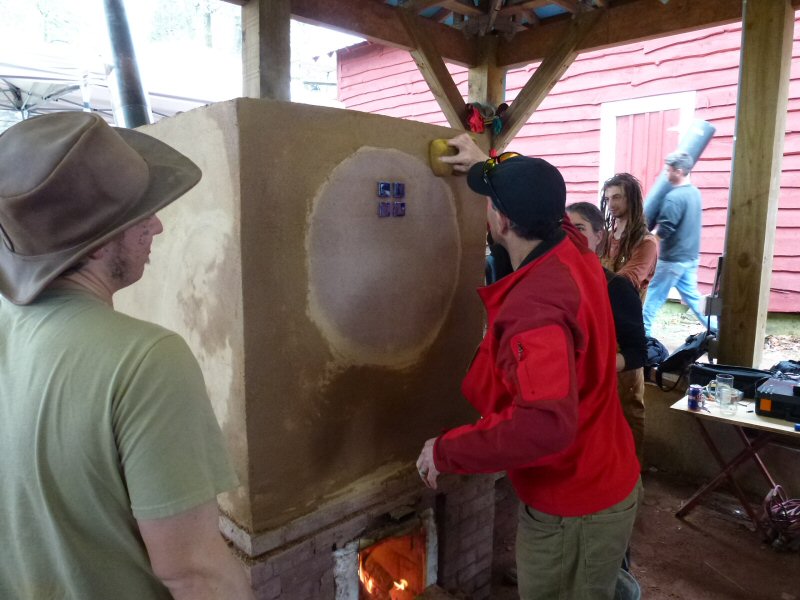
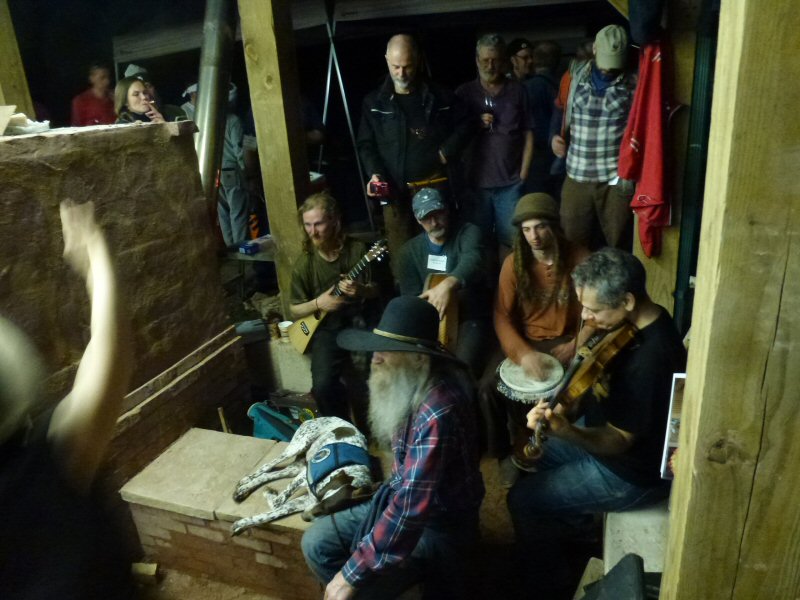
The heater with its warm benches was a big focal point for our annual pizza party.
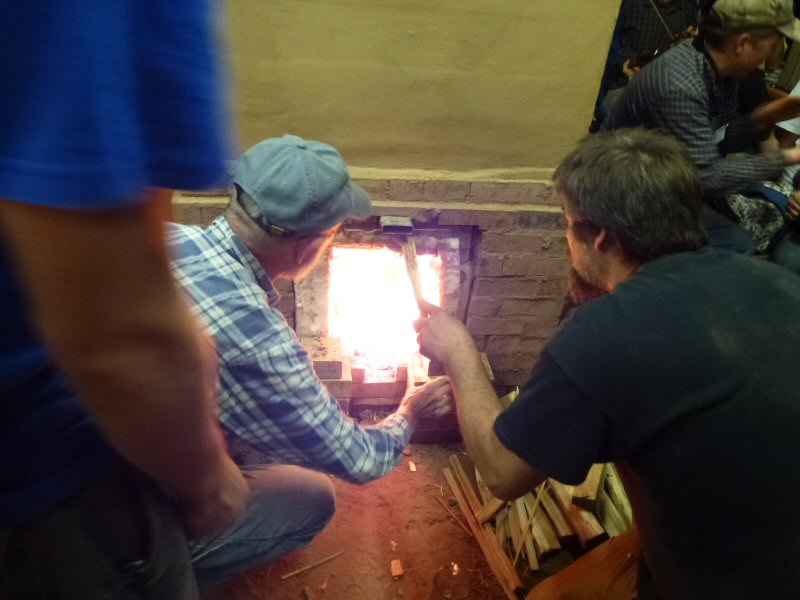
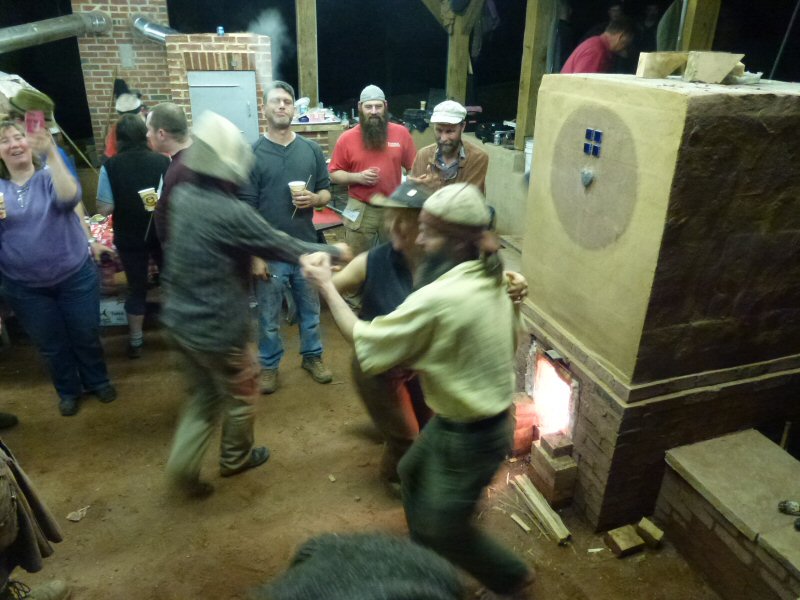
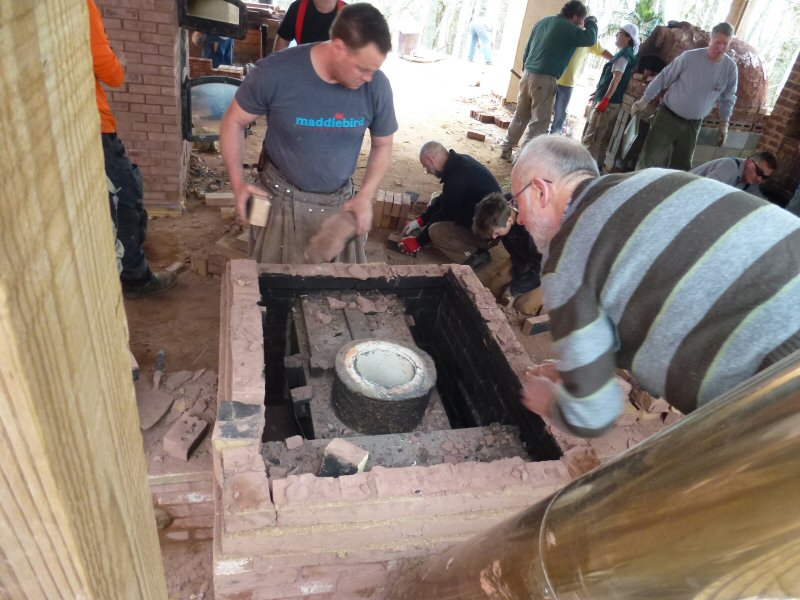
Next day: demolition and inspection.
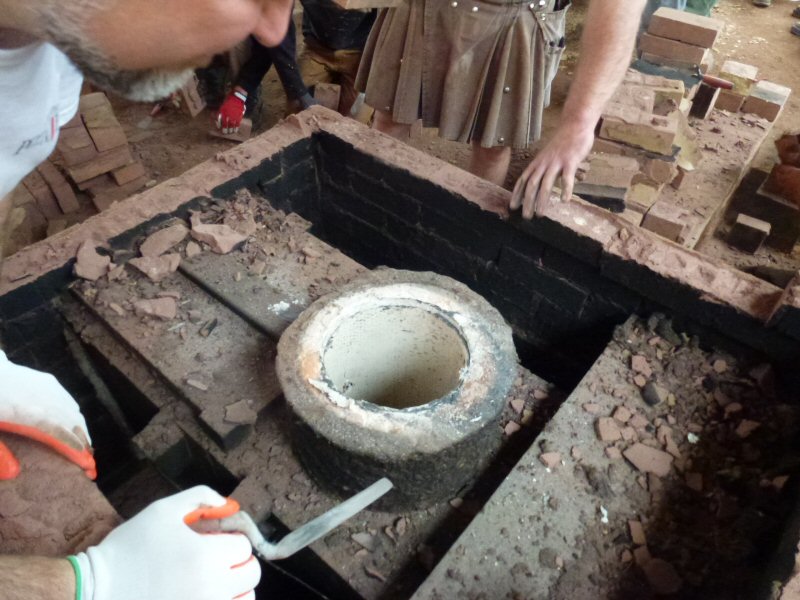
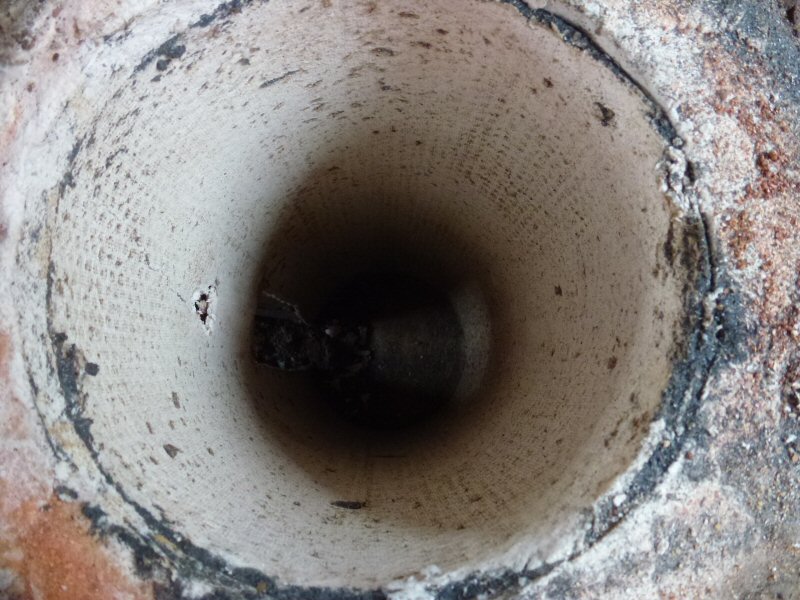
A bit of damage to the riser where it was notched, creating a very thin section.
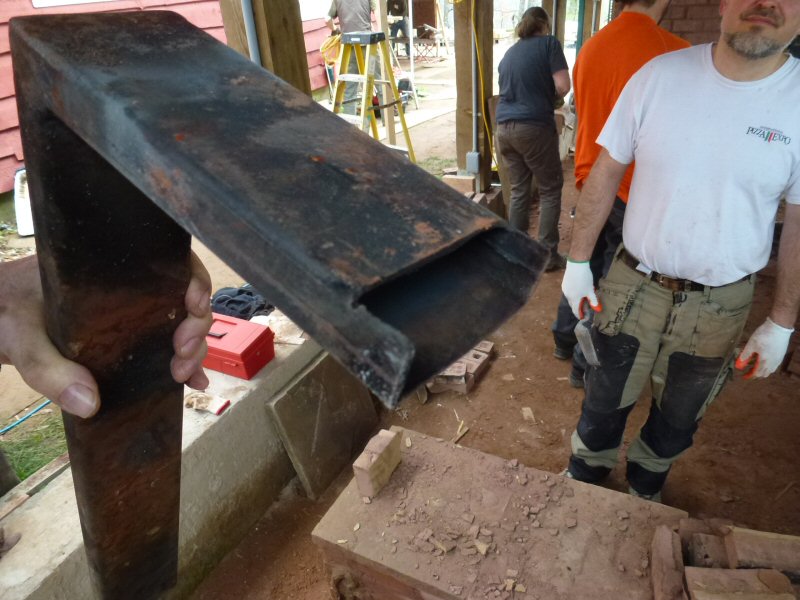
P tube showed no wear.
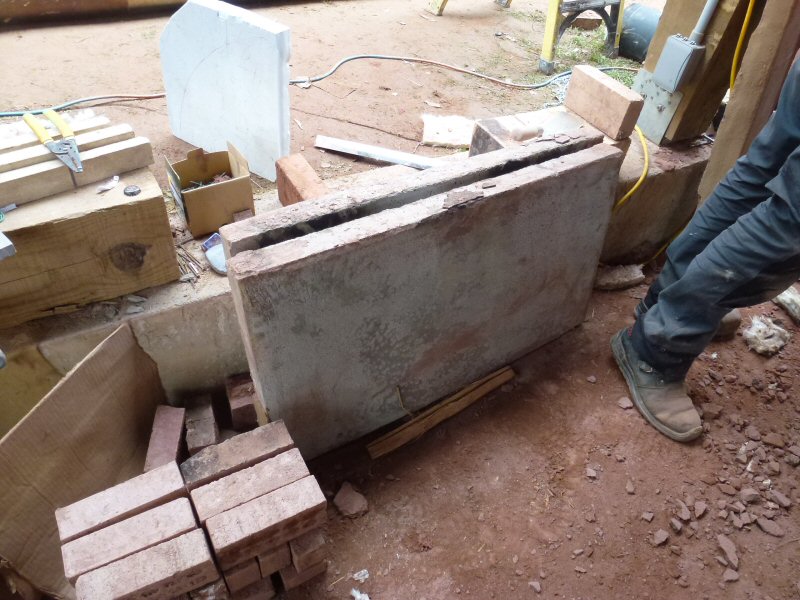
Castable slabs were good, also.
Also see report by Leslie Jackson:
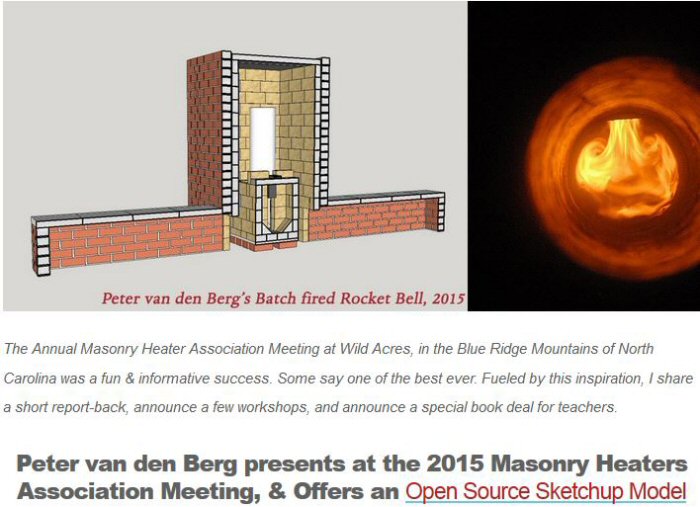
See also:2014 Photo Report
2013 Photo Report
2012 Photo Report
2011 Photo Report
2010 Photo Report
2009 Photo Report
2008 Photo Report
2007 Photo Report
2006 Photo Report
2004 Photo Report
2003 Photo Report
2002 Photo Report
2001 Photo Report
2000 Photo Report
1999 Photo Report
1998 Photo Report
1997 Photo Report
This page was last updated on May 8, 2015
This page was created on April 24, 2015
Back to:
