
2011 MHA Annual Meeting
Five
Run Heater with Rear White Bake Oven
with Norbert Senf and Brian Klipfel
Photo Credits: Norbert Senf
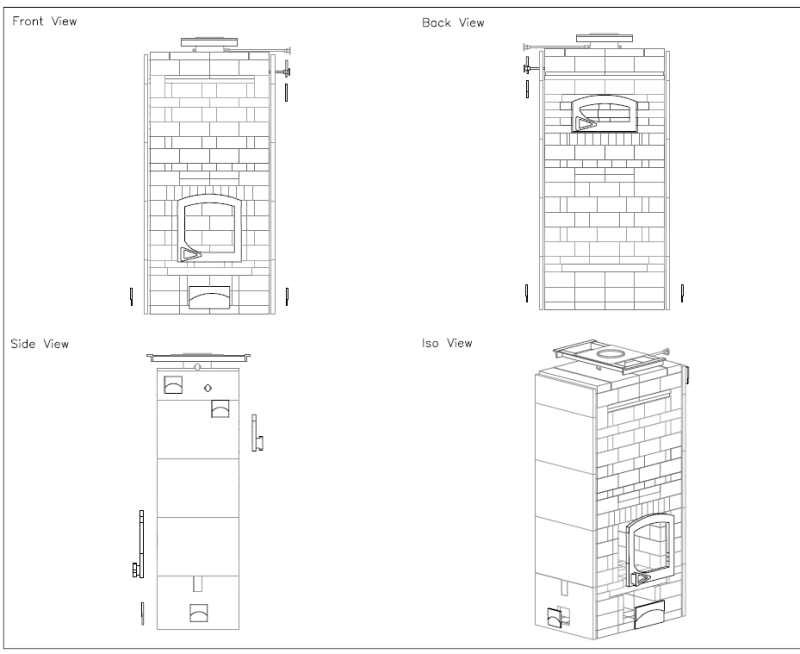
Drawings by Jason Champion, Mid-Atlantic Masonry Heat
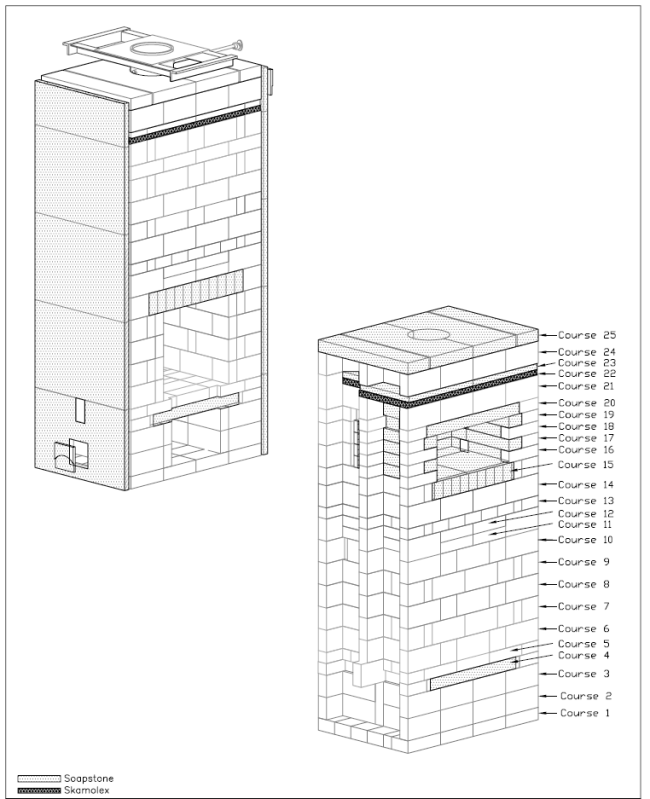
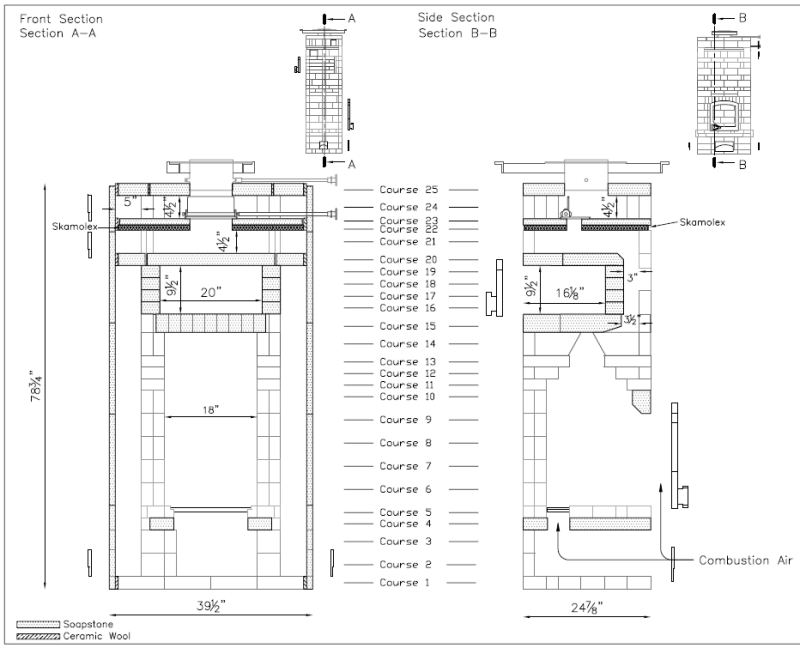

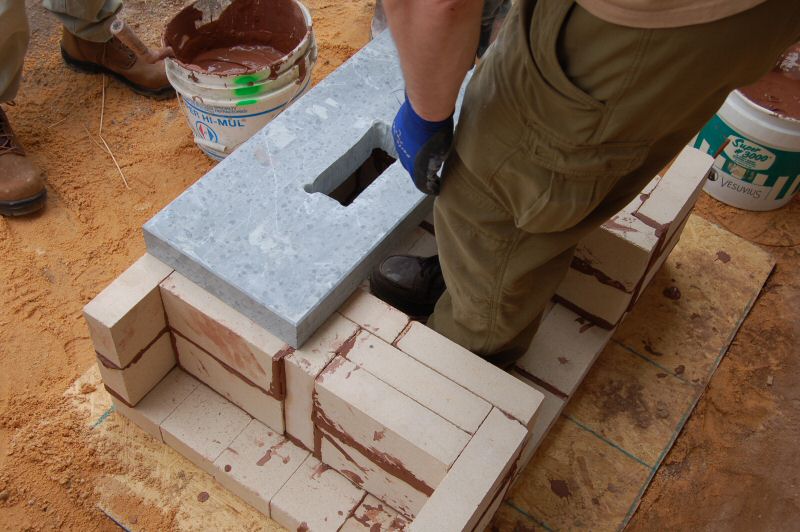
This heater has an improved rear white oven.
It is designed to minimize the amount of firebrick cutting. Soapstone slabs are used to eliminate the need for
refractory castings.
Soapstone slab heat exchange side panels were compared with thin firebrick panels
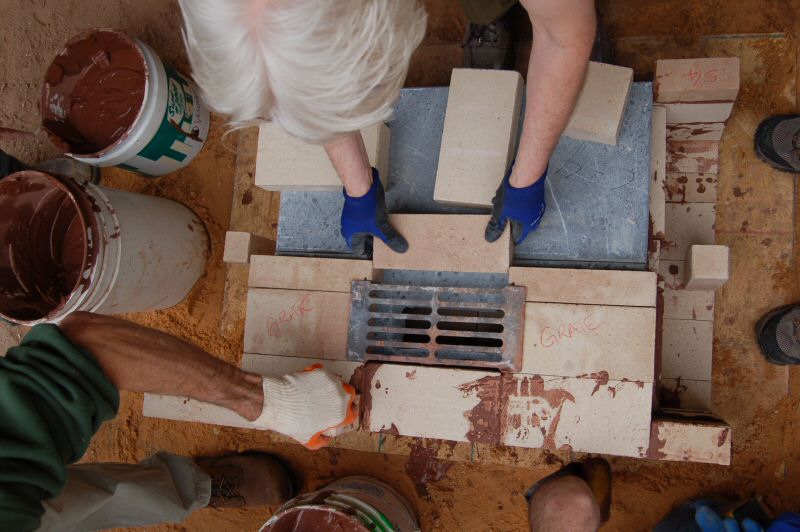
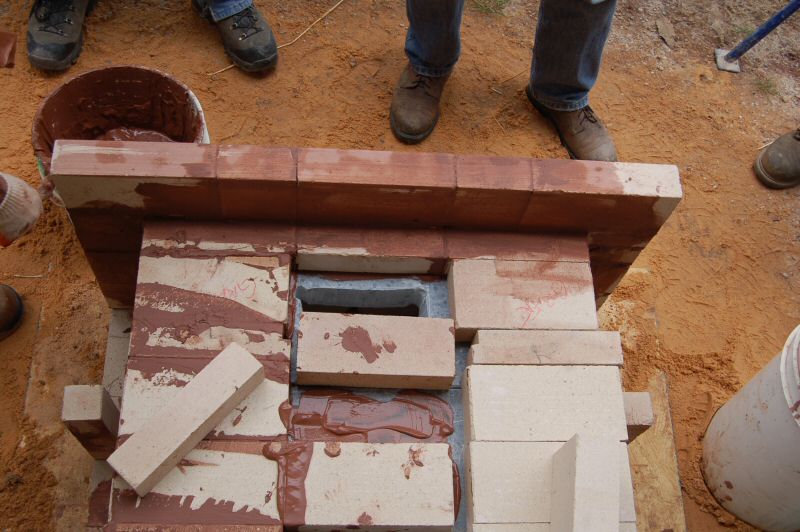
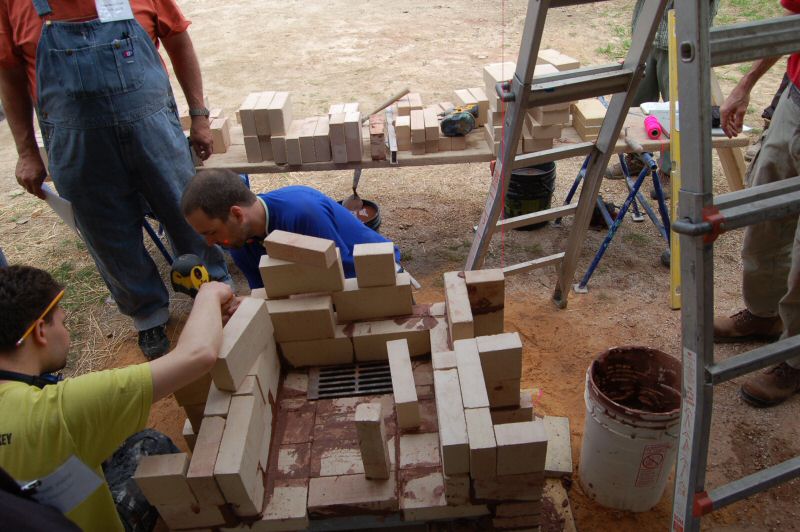
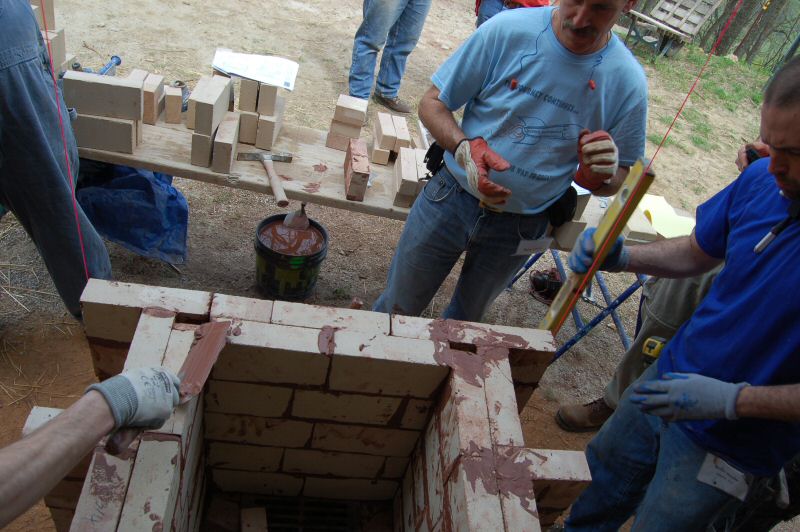
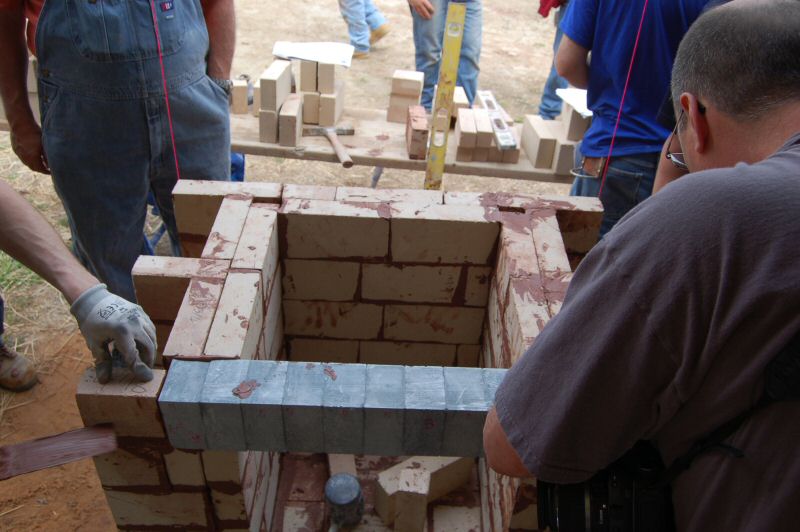
Bolted soapstone firebox lintel
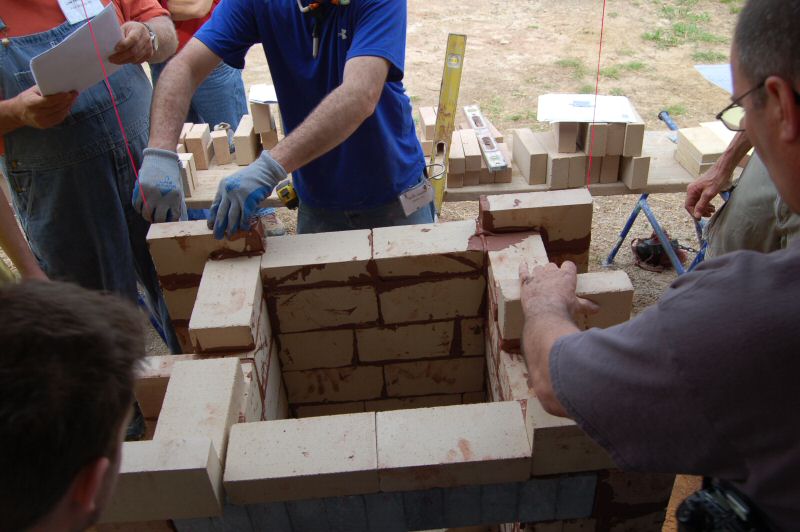
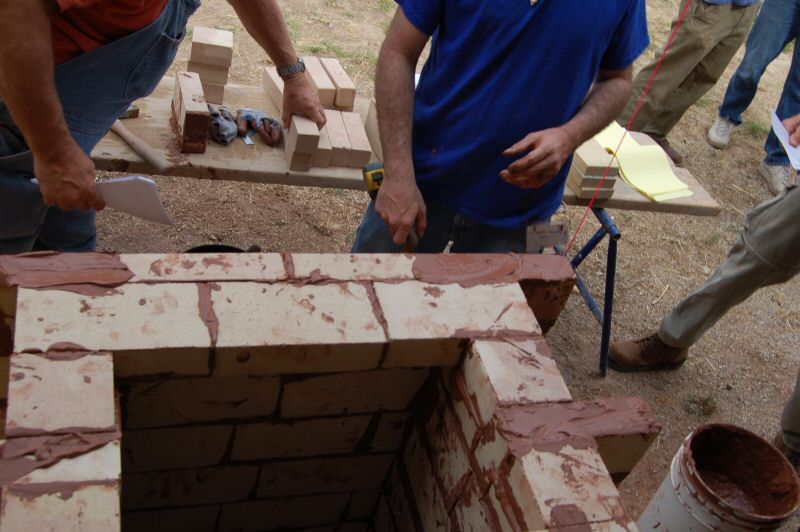
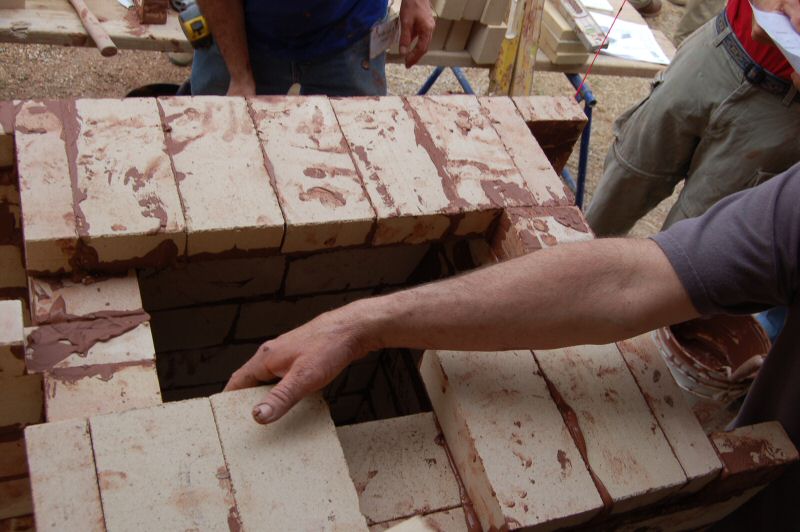
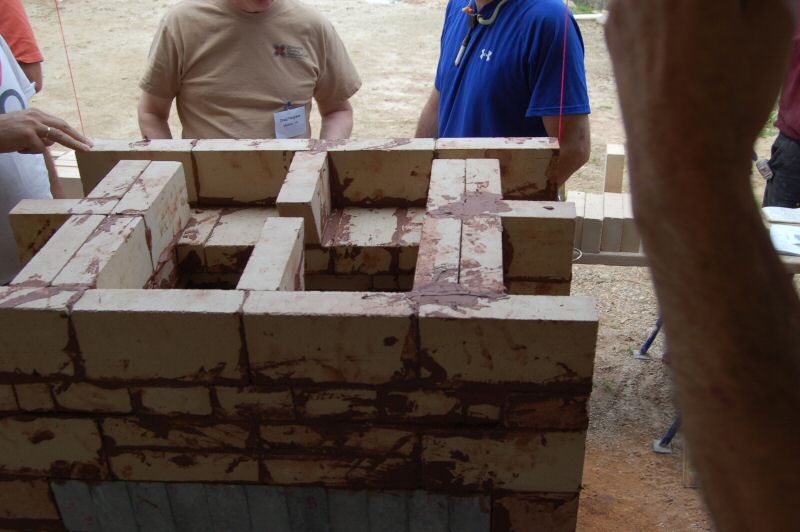
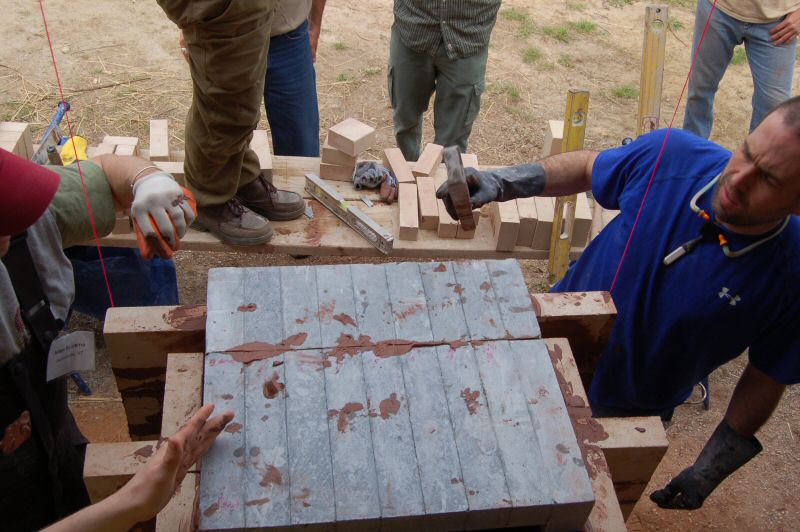
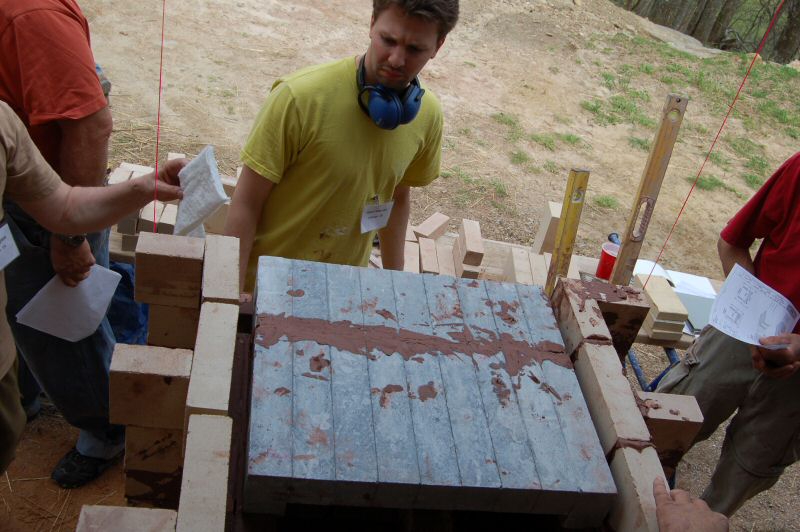
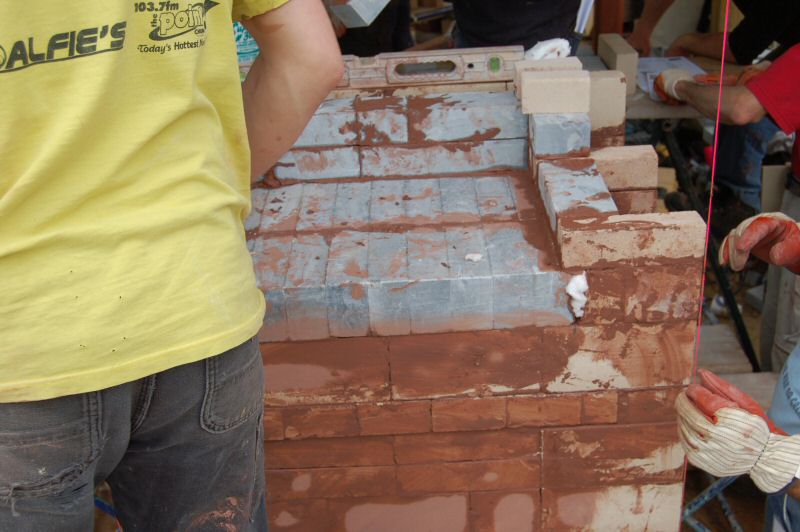
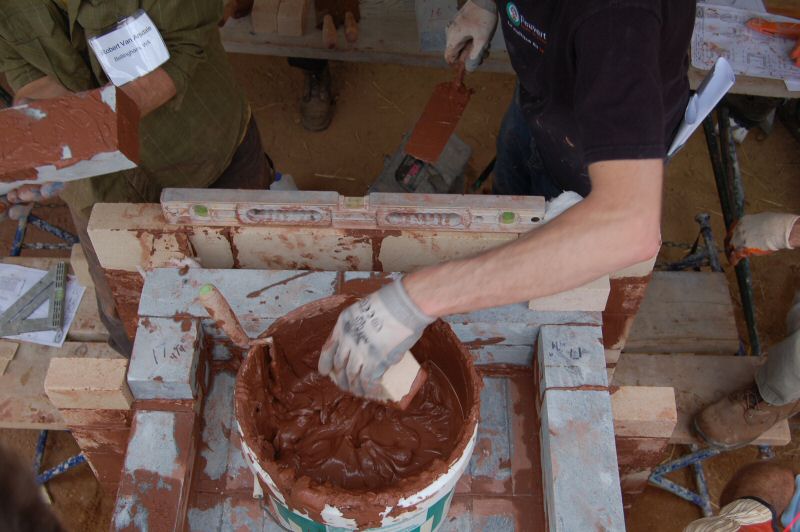
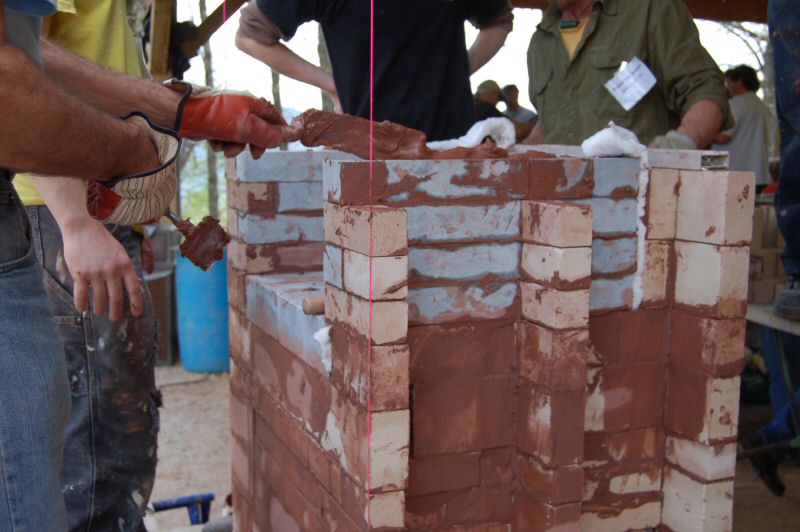
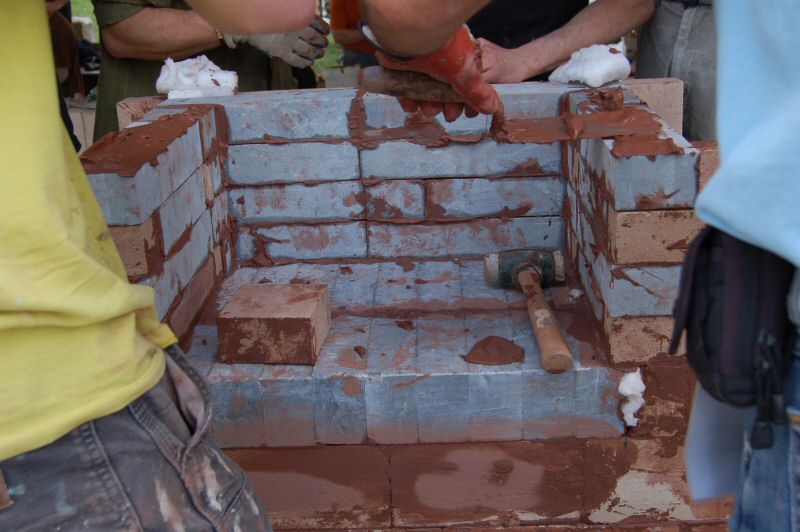
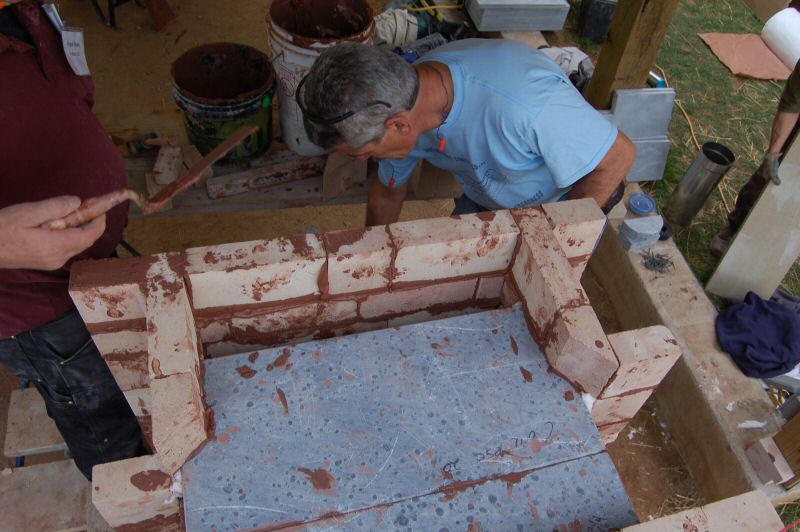
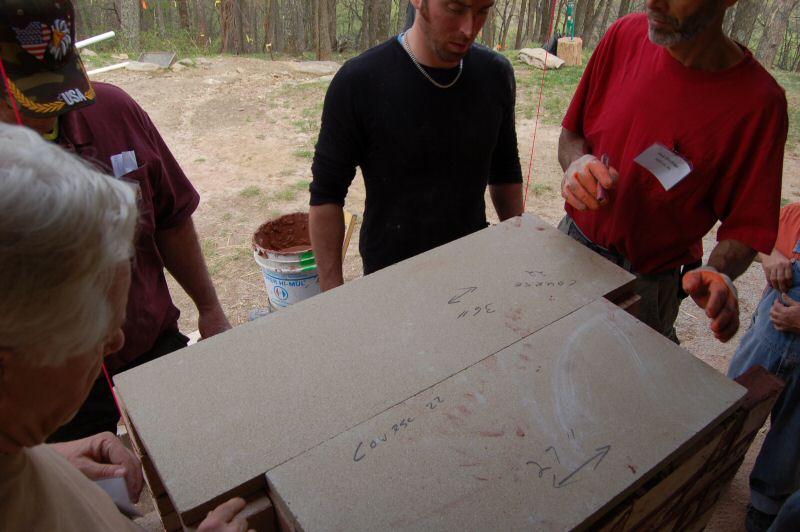
Skamolex insulating panel forms the lid for the downdraft plenum, above the oven ceiling. The Skamolex helps
prevent oven heat from bleeding into the soapstone panel above.
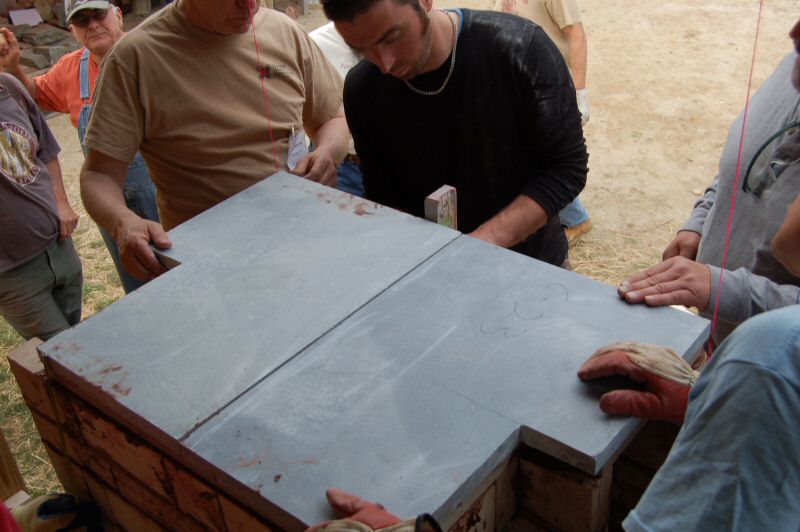
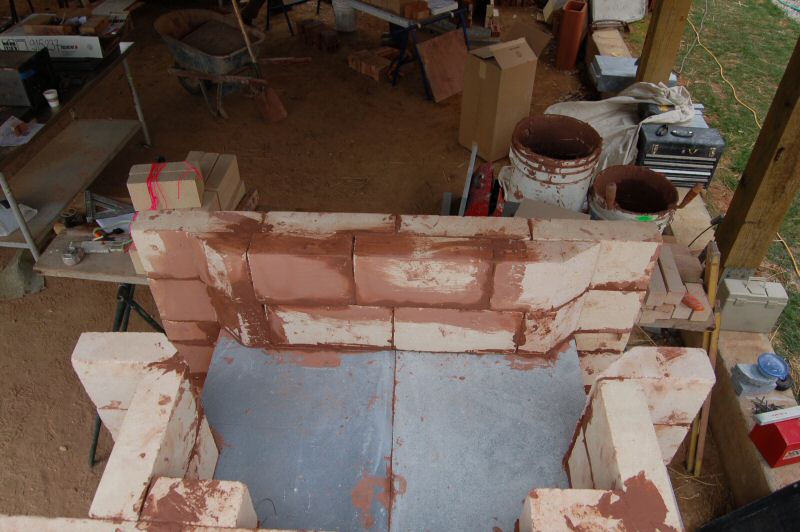
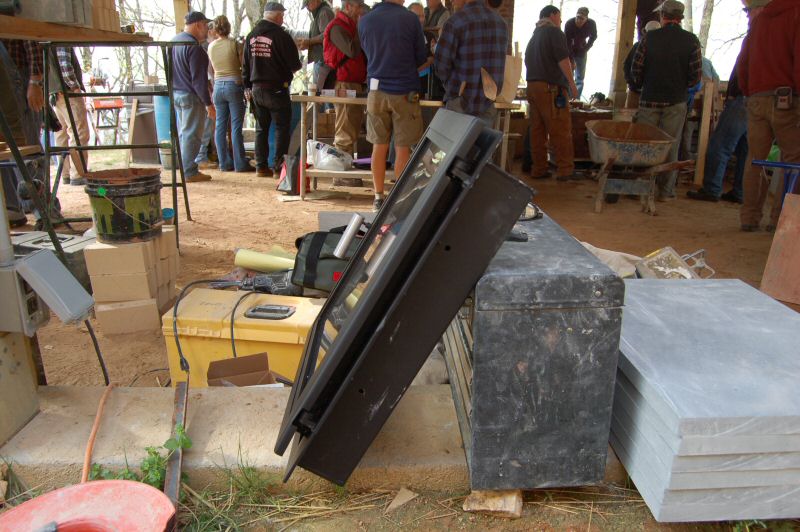
Prototype of a new airframe door by Eric Moshier. It worked very well on this heater, and the fire started clean,
even in a brand new cold, wet heater.
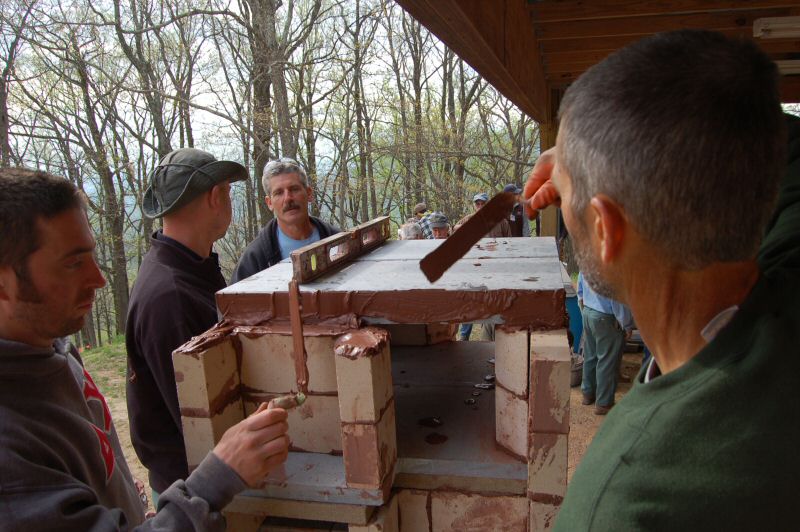
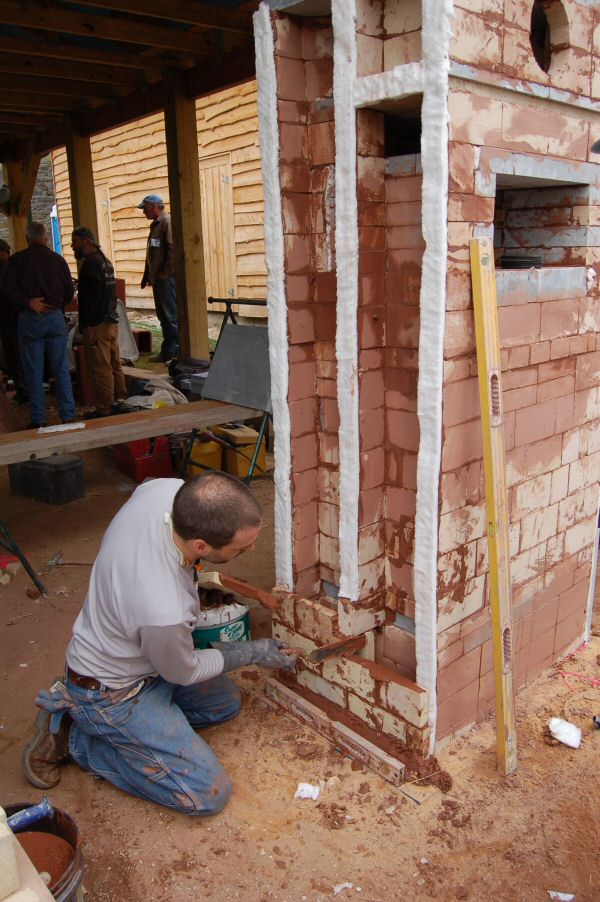
Brian Klipfel builds the right side heat exchange panel from firebrick splits. Note the ceramic
fiber expansion joints.
When the heater was fired, the soapstone side ran about 20 to 30 degrees warmer than the
firebrick side. Both panels were about 1.25" thick.
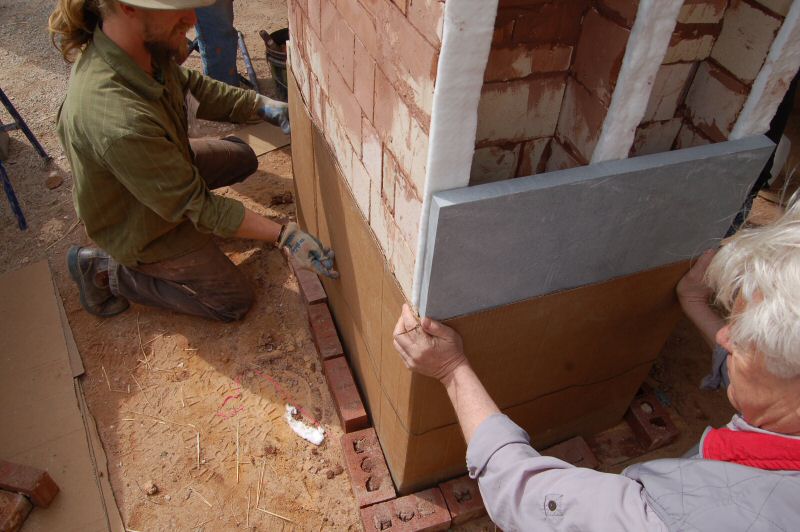
Soapstone heat exchange panles are installed as the heater core is wrapped with cardboard.
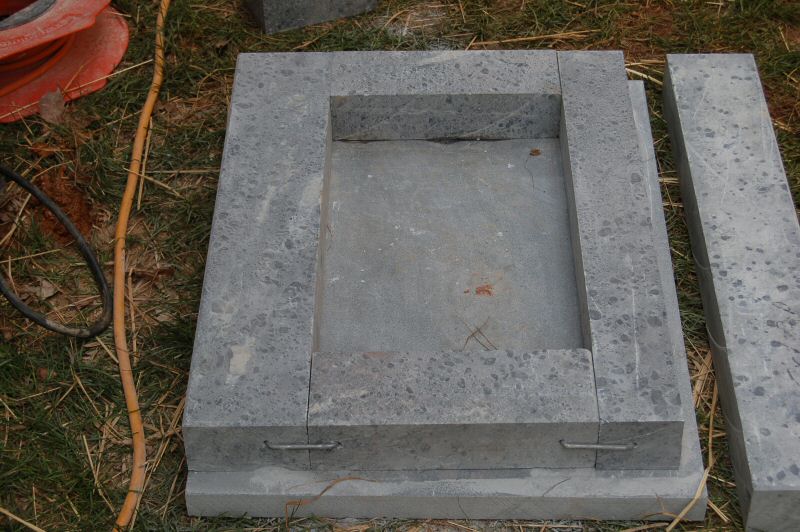
Soapstone frame to hold the bakeoven door.
(Not shown) A similar frame was used to hold the firebox door.
The firebox door was a prototype for a new design be Eric Moshier, which incorporates an air frame is able to
supply all of the comustion air, independently of the heater core construction.
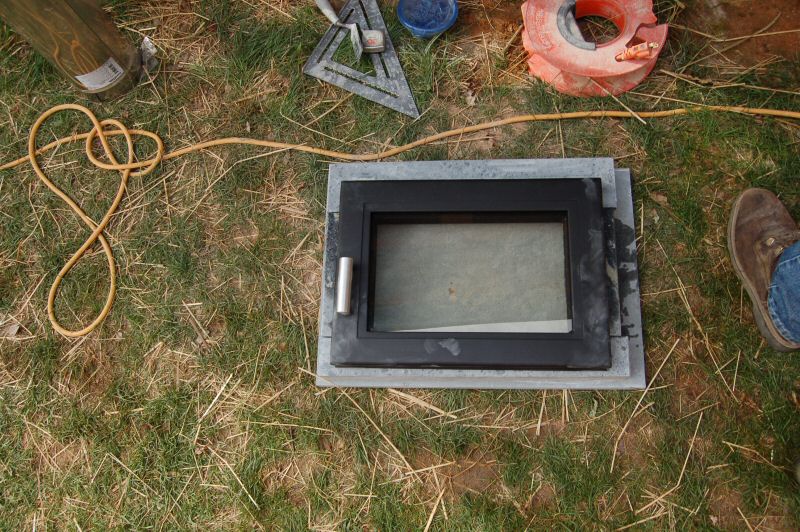
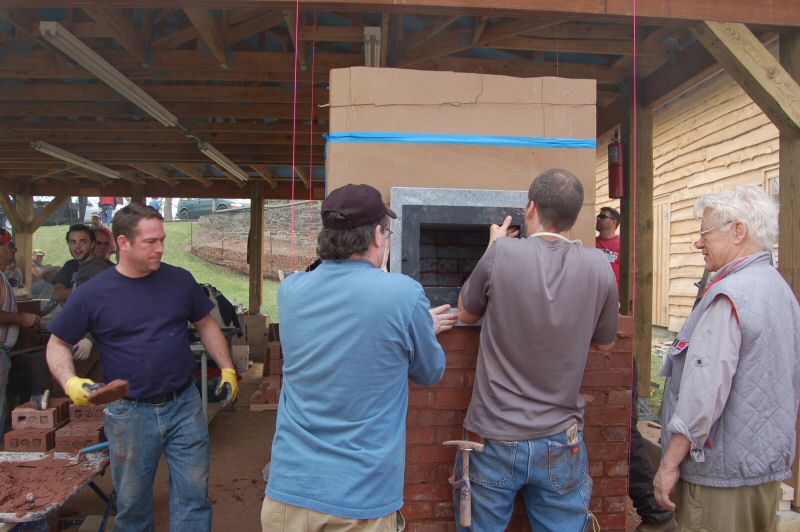
Mounting the oven door and frame
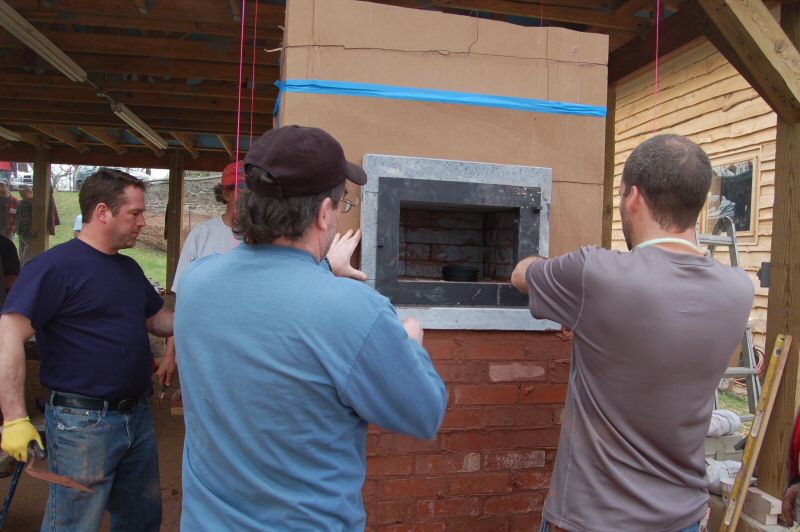
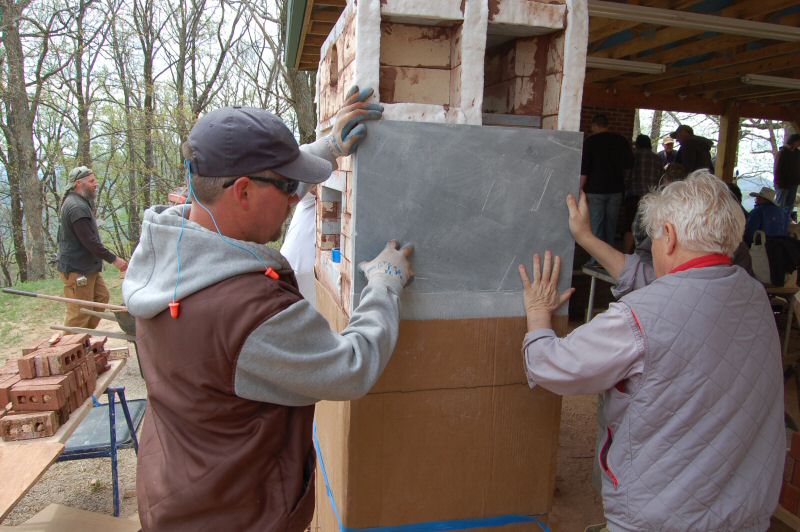

There is a space between the face brick and the cardboard, which is slushed tight with mortar.
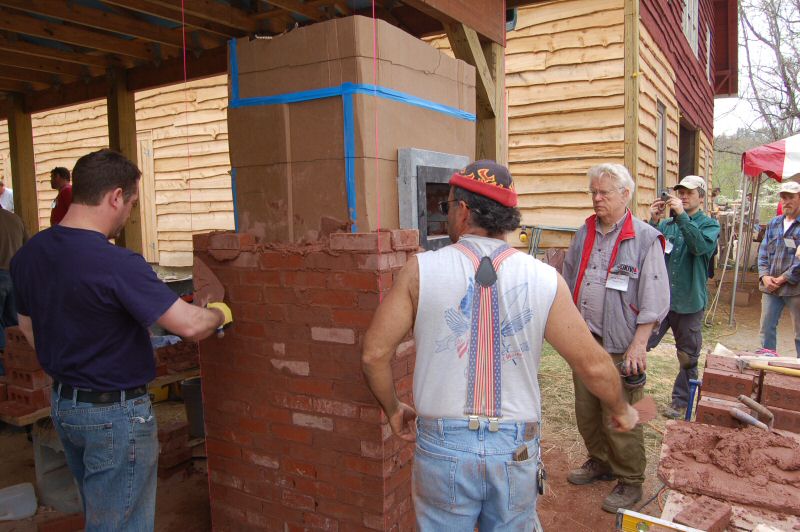
Almost finished.
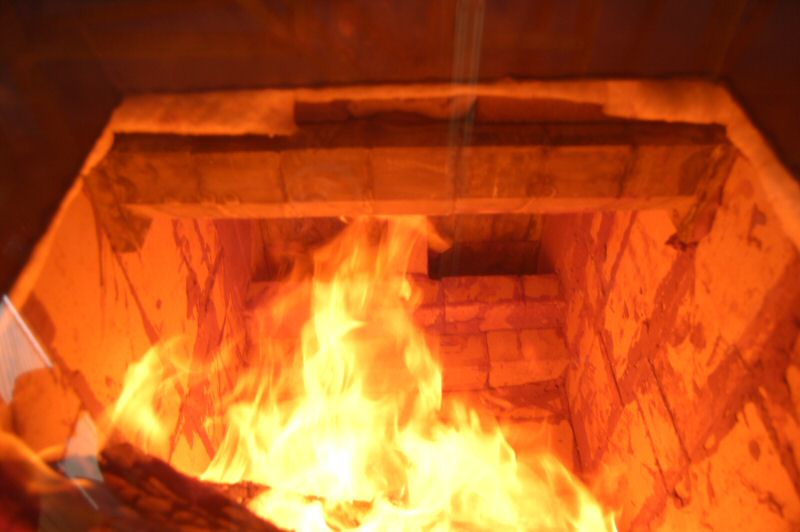
The heater was fired up immediately to dry it out. View through the firebox door, towards the throat.
The throat is in the front. You can see some flames heading towards the rear, to the bypass openings that help to
even out the temperature in the oven floor.
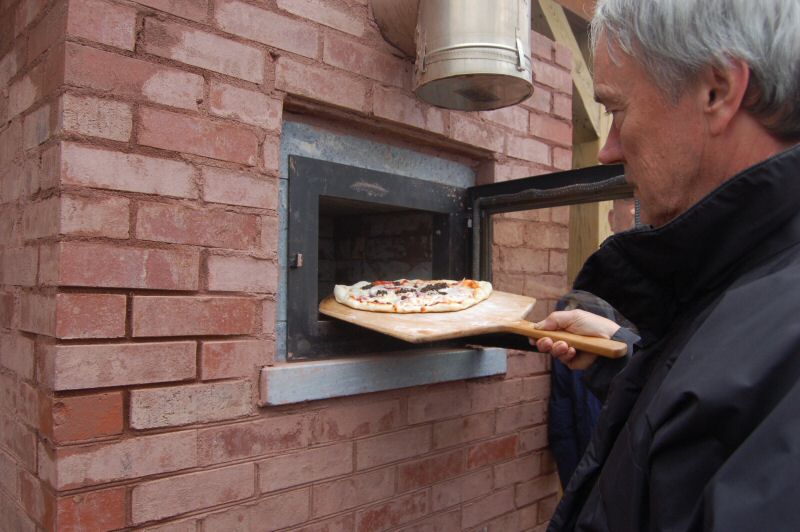
Pizza party the next day. The heater had been fired pretty hard, perhaps 200 lbs of wood over 2 days.
The oven got very hot, in the 800F range. Hottest spot measured was at the rear of the oven floor, at 935F.
We tried to cool it down, but the floor was a bit hot for pizza. A layer of firebrick splits over the soapstone floor would
have helped.
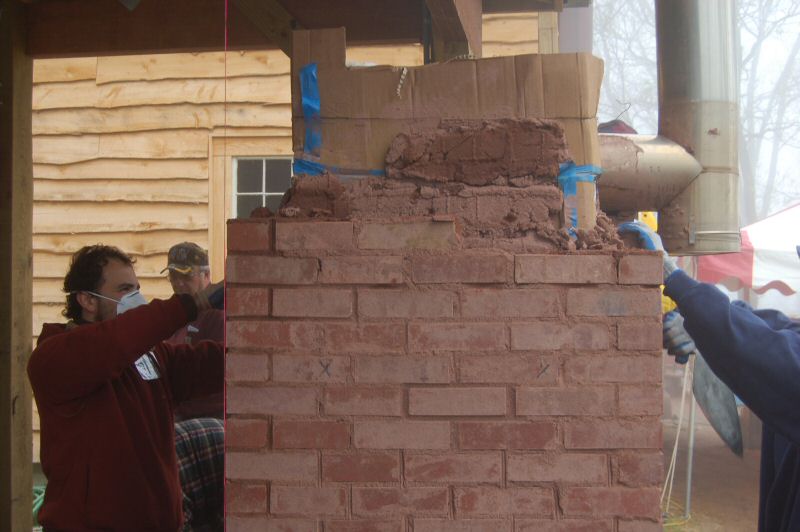
Teardown on Saturday. The materials were still hot, and gloves had to be worn.
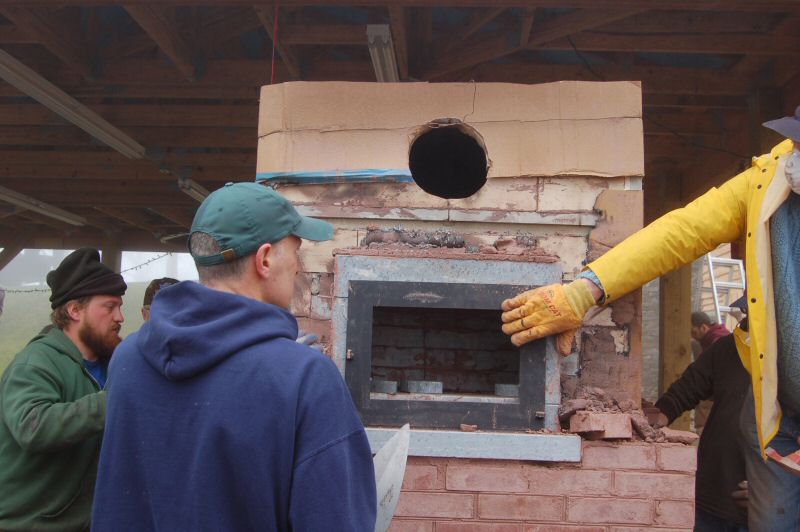
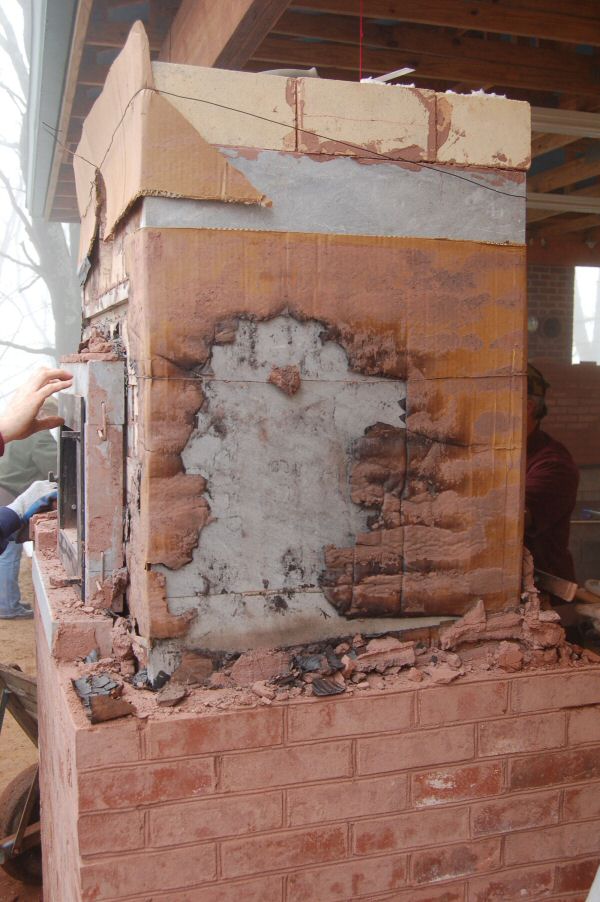
Burn pattern in the cardboard
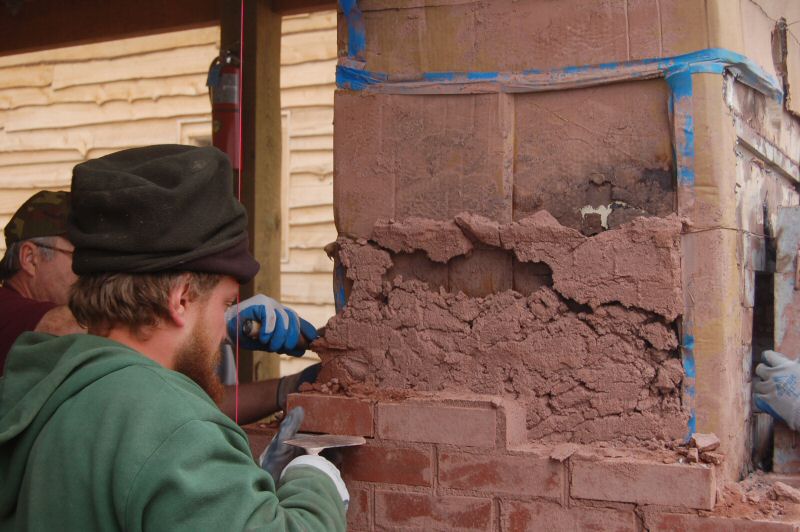
Firebrick
side. Note the slush is not well consolidated - during construction the
bricks were wet and bulging out, so the slush required
extreme care. Normally, it is not a problem.
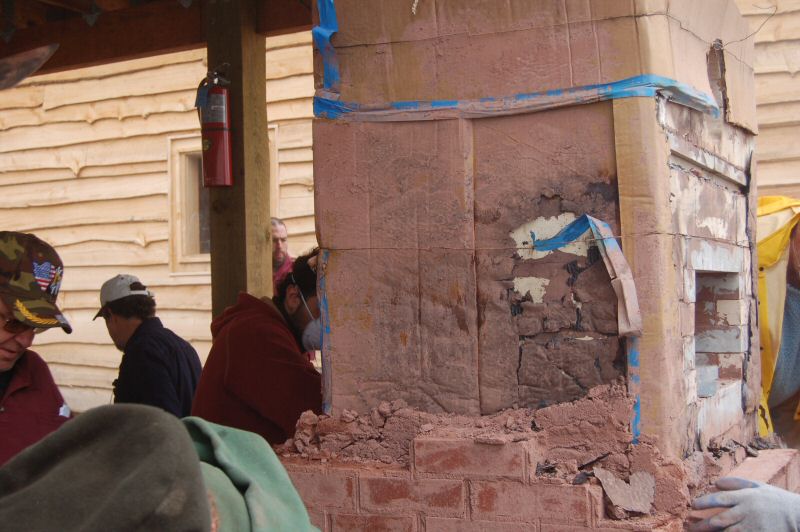
Burn pattern - compare with same view, above.
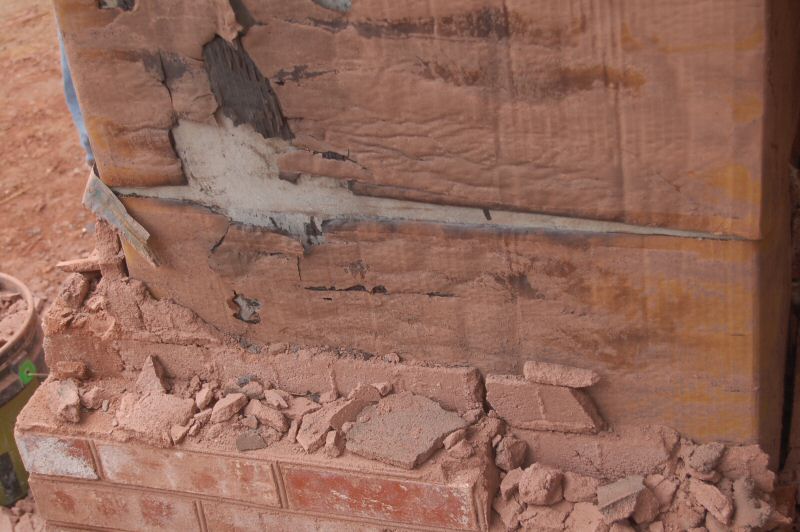
Rear
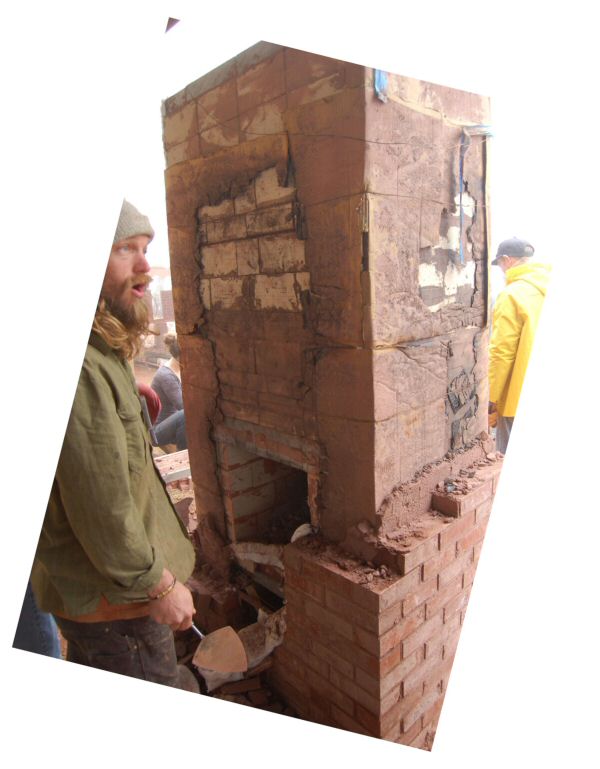
Front and right side.
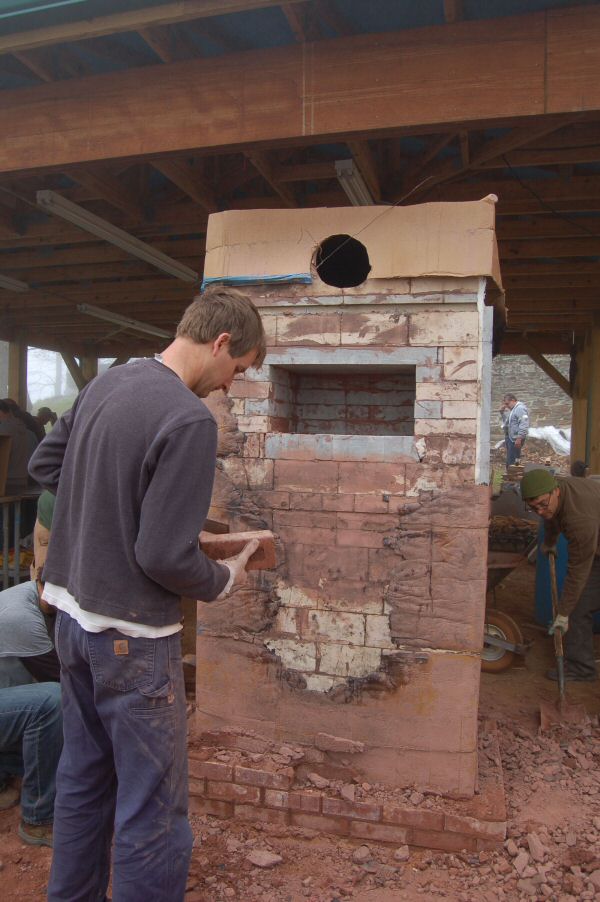
Rear
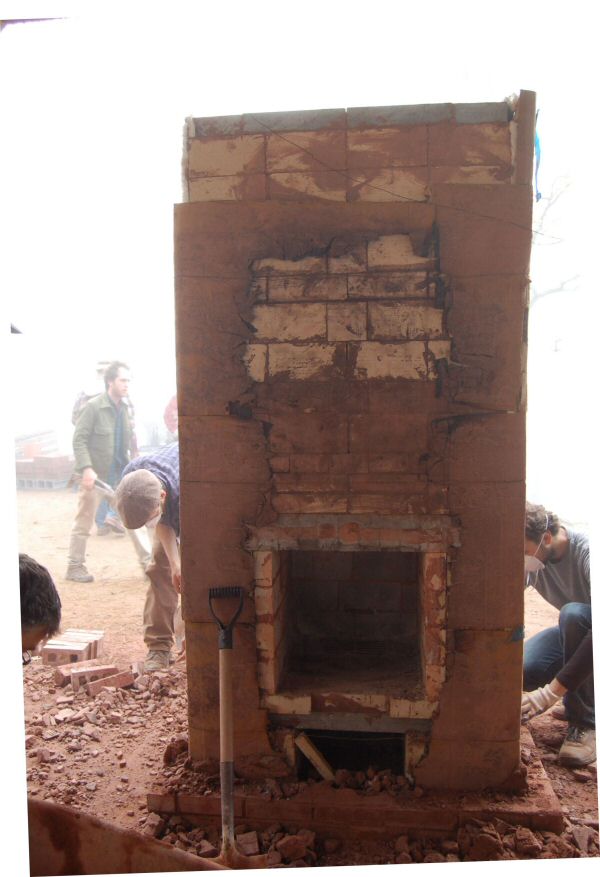
Front
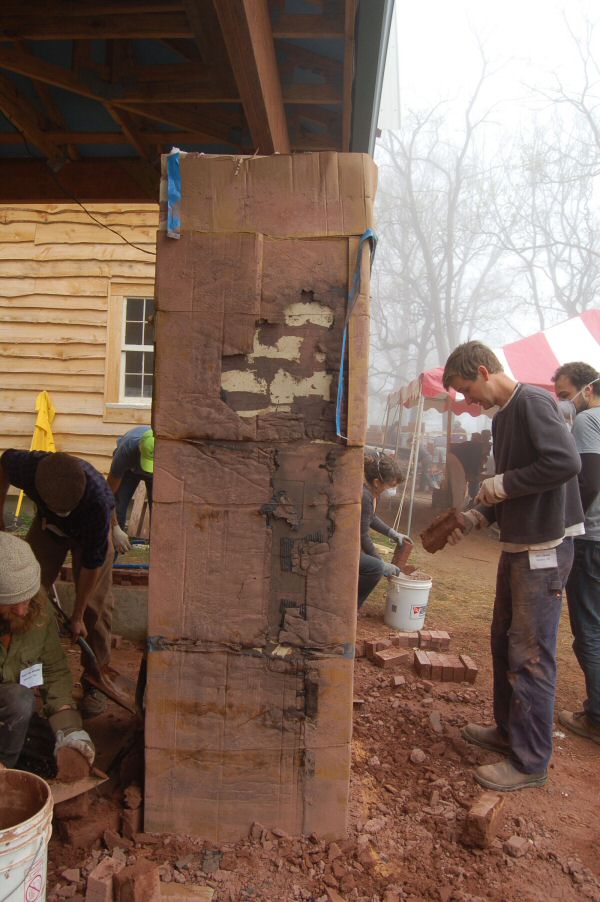
Right. Compare with left, below.
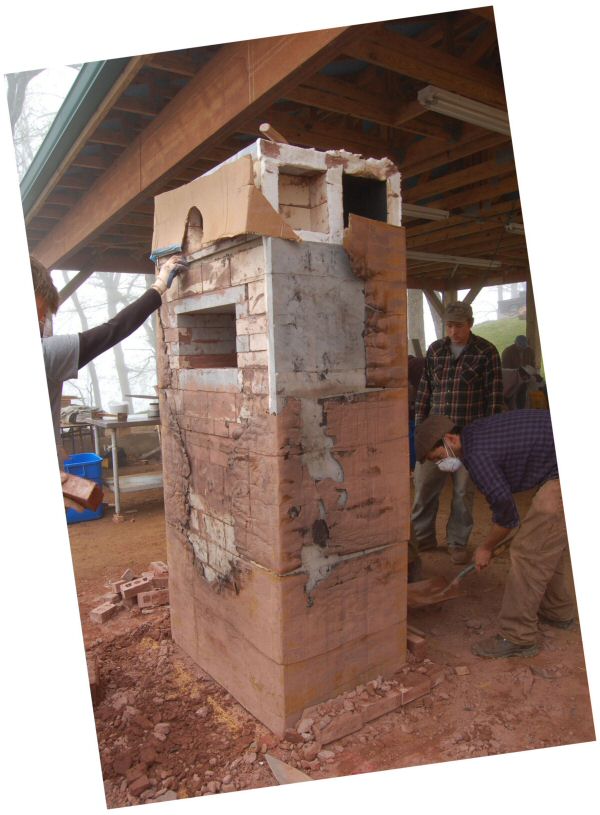
Soapstone seems cooler at the bottom of the downdraft channel, compared to firebrick.
Perhaps because gases have cooled sooner from extra heat exchange.
However, this was not consistent with the outside skin temperature readings, so a bit of a mystery.
Perhaps the degree of contact of the cardboard is an issue, and air pockets may matter.
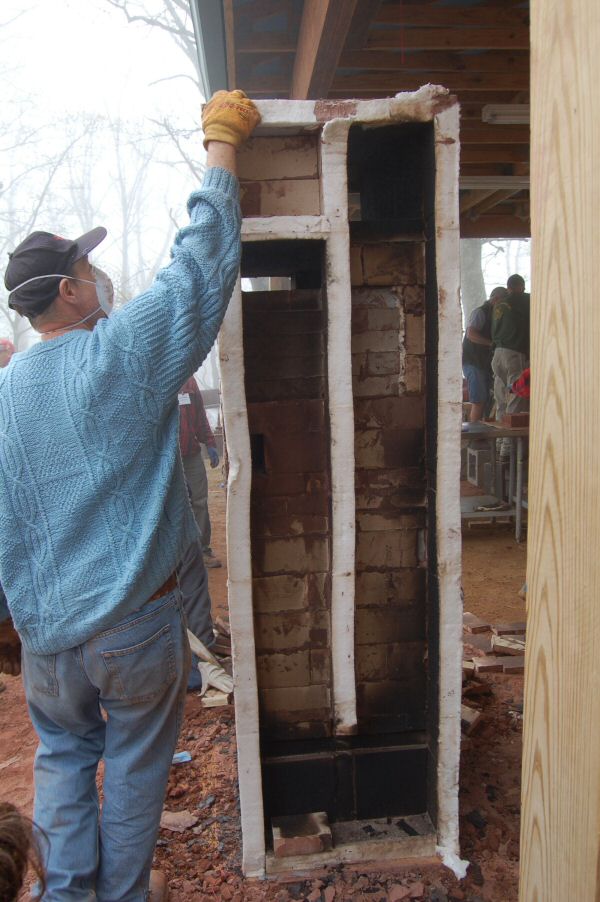
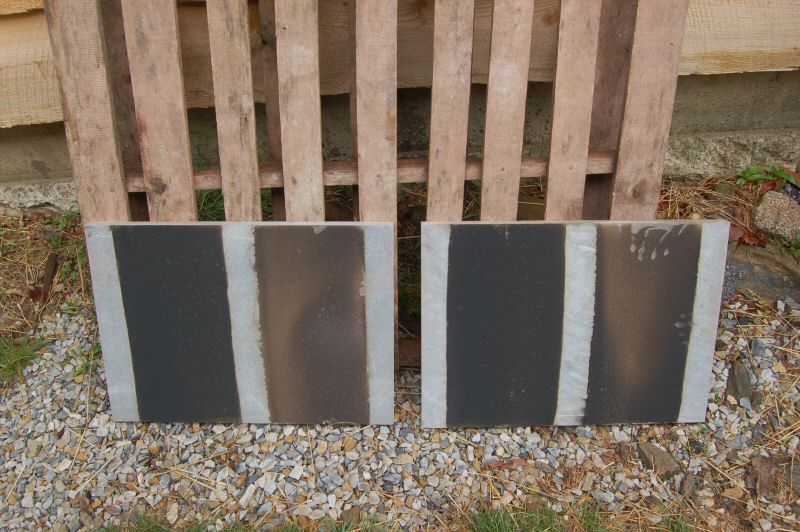
Soot patterns on the heat exchange panels. The top panel sits on the left, and the brown side is the hotter, or
downdraft side. On the right panel, you can see the downdraft side turning darker towards the bottom.
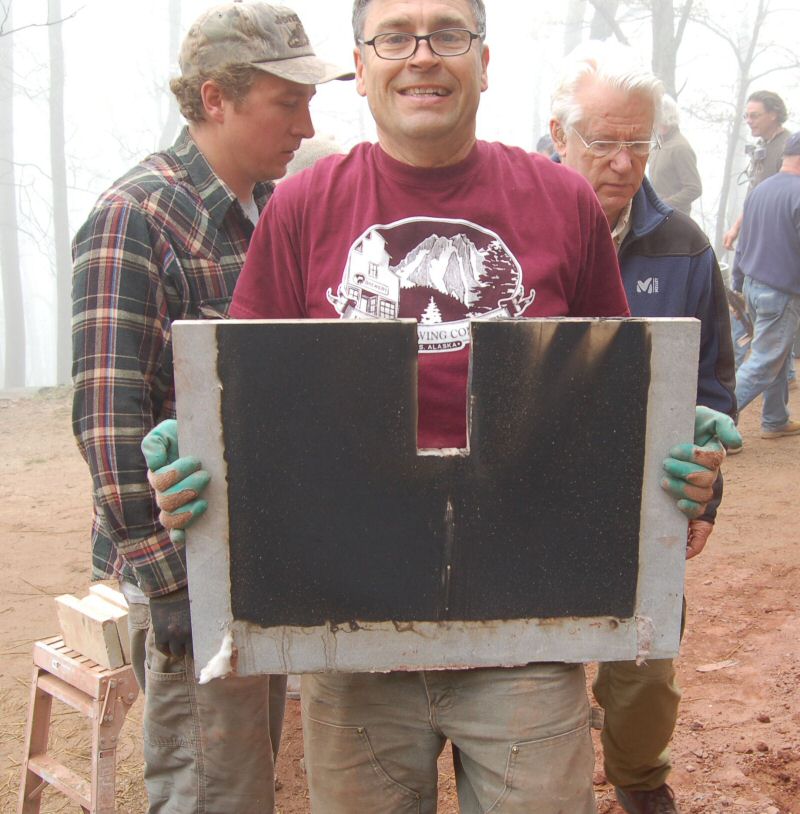
Bottom panel.
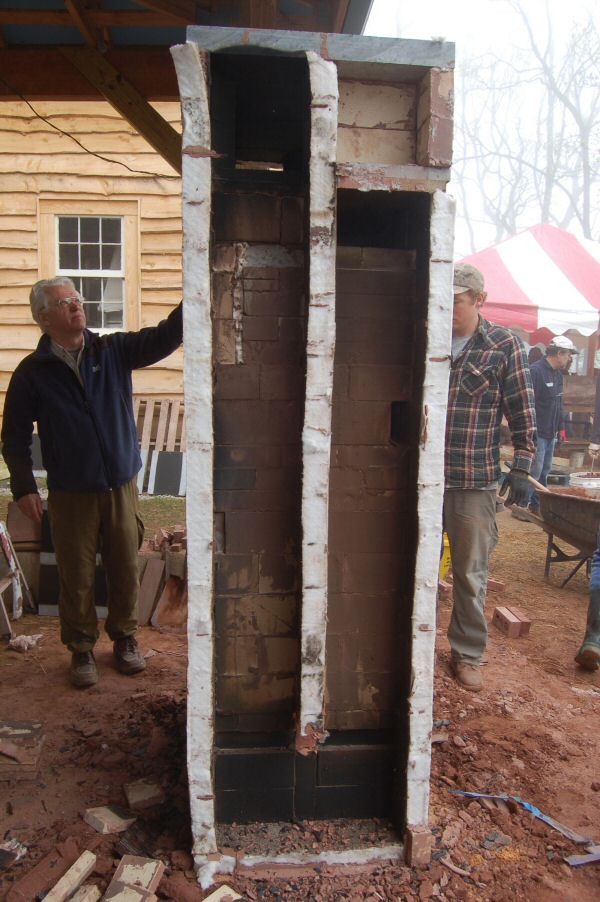
Firebrick side.
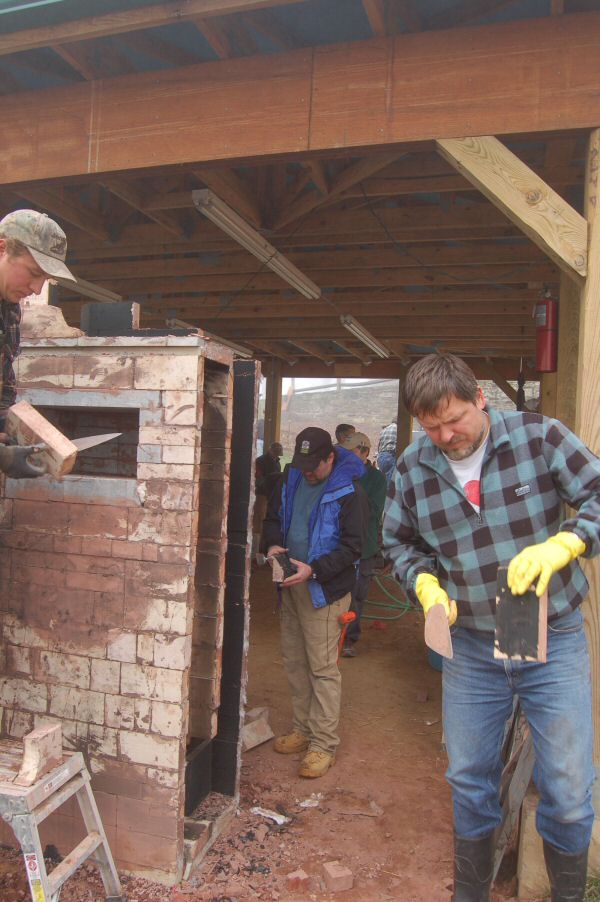
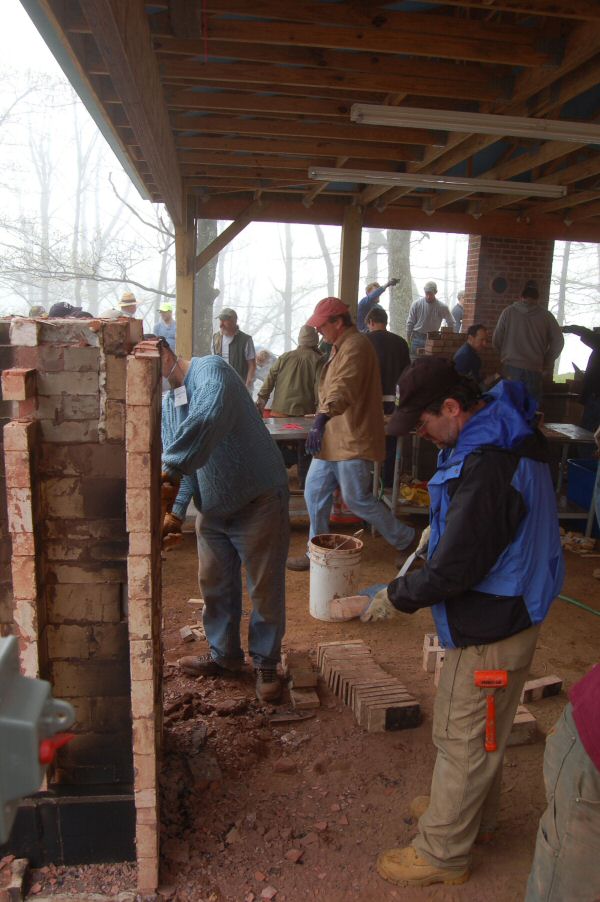
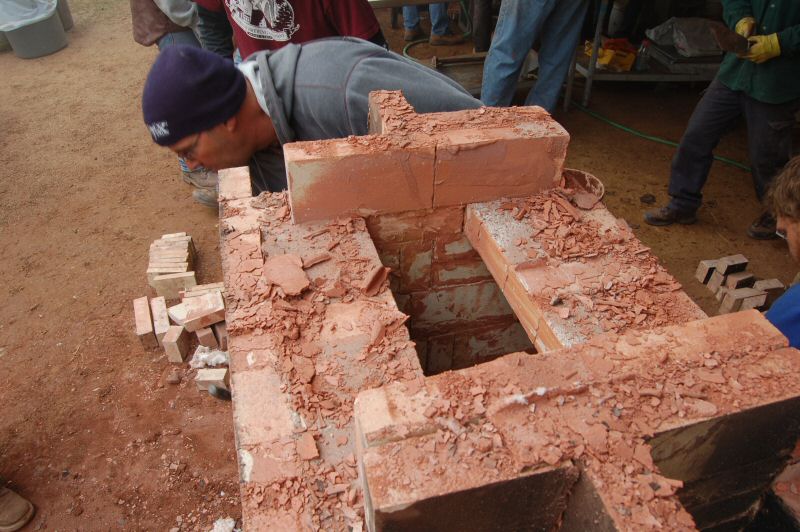
See also,
2010
Photo Report
2009
Photo Report
2008
Photo Report
2007
Photo Report
2006 Photo Report
2004 Photo Report
2003 Photo Report
2002 Photo Report
2001 Photo Report
2000 Photo Report
1999 Photo Report
1998 Photo Report
1997 Photo Report
This page was last updated on April 28, 2011
This page was created on April 24, 2011
Back to:
